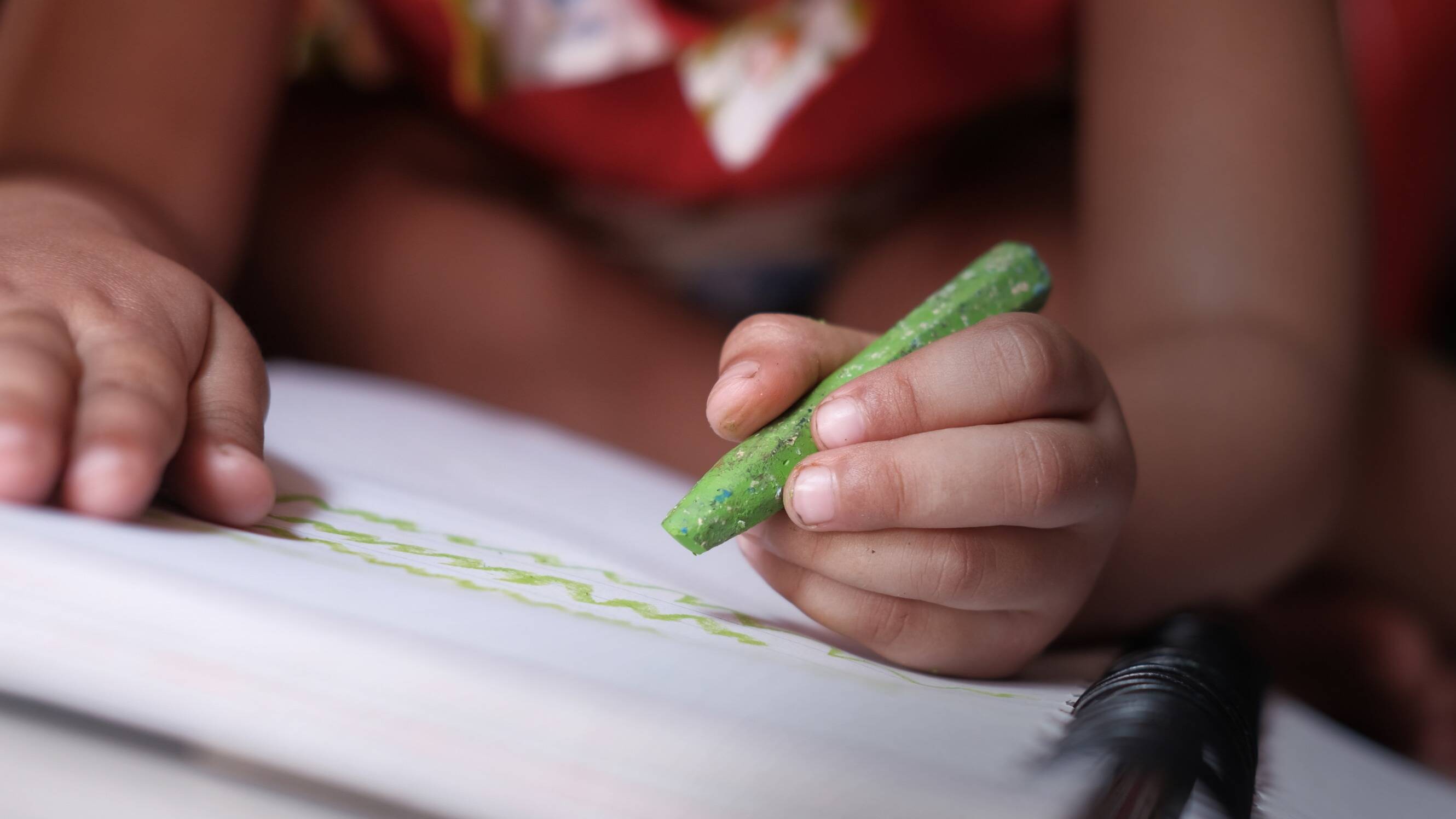
Developing Sustainable packaging Solutions
We are determined to improve the lifecycle of our packaging products one step at the time.
Sustainable materials
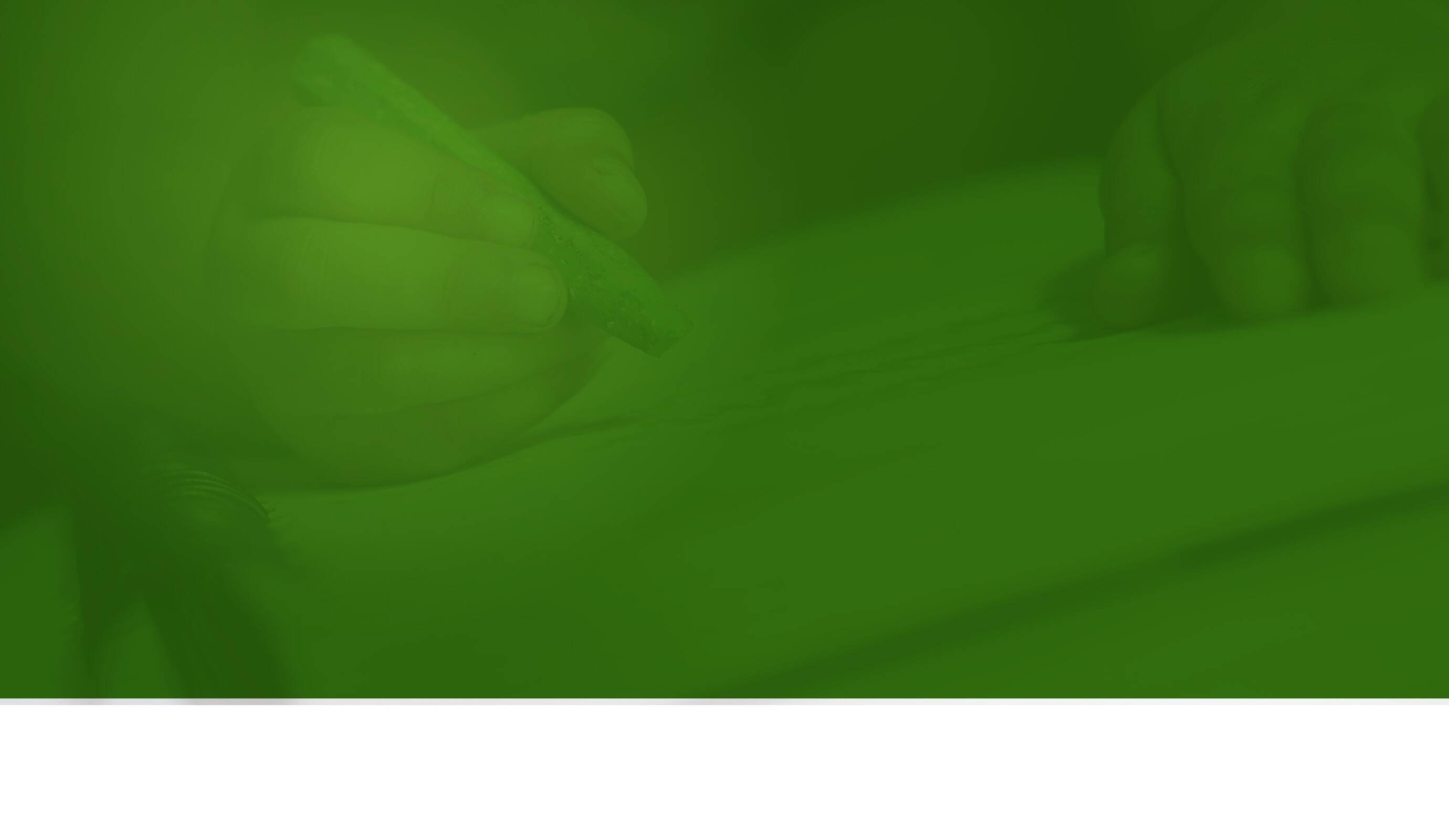
GRI 301: 103-1, 103-2, 103-3
Sustainable solutions 2020: 103-1, 103-2, 103-3
Sustainable materials
Solutions
To minimise the waste related to our packaging, together with our Partners, we analyse, experiment with and optimise:
Back to top


Scroll down
By 2022, we will have minimised the waste associated with our packaging.
Target
Together with its partners, LC Packaging is actively testing the use of recycled PP (rPP) for the manufacture of new big bags (FIBCs). We have already successfully produced a bag containing 20% rPP from our own PP process waste. Together with our Partner Starlinger, we have produced a 50% rPP bag, including rPP made out of used LC Packaging bags. 39% of the total amount of kgs material used in our packaging are recycled input materials. This compared to 43% in 2019. Our cardboard packaging consists of 85% recycled content.
Recycled content
LC Packaging products consist of roughly 3 materials: PP/PE (plastics), jute and cardboard. 50% of our packaging solutions is made out of renewable materials and 100% out of recyclable materials. In total, we used approximately 87 million kilos of material for our products in 2020 (88 million in 2019), of which 50% cardboard and 45% PP/PE. Compared to 2019, our use of plastic materials has decreased by 1.3%.
Materials
In 2020, we distributed more than 360 million packaging solutions (337 million in 2019) of which 64% was recyclable. In 2019, we calculated that 98.2% of the packaging distributed was recyclable. In partnership with the Dutch Knowledge Institute for Sustainable Packaging (KIDV), we are in the middle of a deep dive sustainability analysis for all our product groups. Packaging that may theoretically be recyclable, but is difficult to recycle in today’s society, has been identified as non-recyclable in this 2020 report. This explains the decreased percentage of recyclable packaging solutions. The deep dive analysis was conducted to help us define a clear strategy for the upcoming years, with the ultimate goal to make all of our products as circular as possible – starting with 100% recyclable and, where possible, reusable.
Reusable and recyclable solutions
With our GREENBangla recycling initiative, we once again recycled 80% of our virgin PP process waste in 2020. This adds up to 425 mt. Thanks to a state-of-the-art Starlinger Recycling Machine, 20 high-quality jobs were created for the purpose of upcycling our process waste. In total we recycled 29% of our total global waste production in-house in 2020.
More data in our 2020 Solutions Report.
Reducing process waste
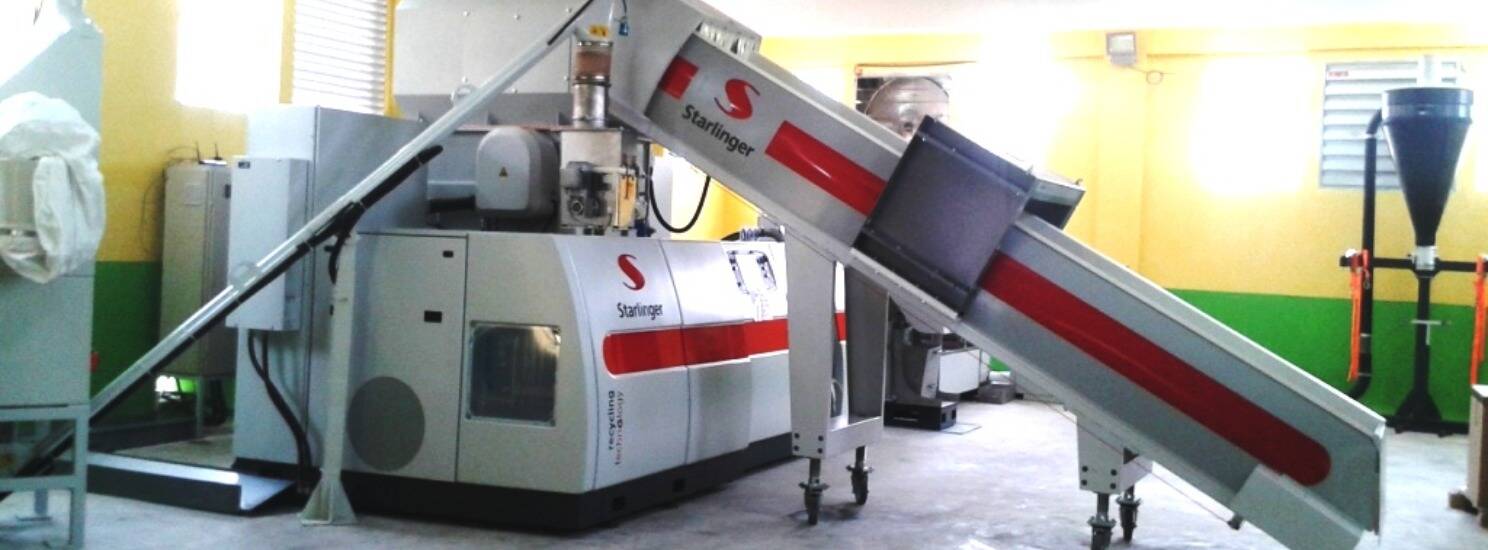
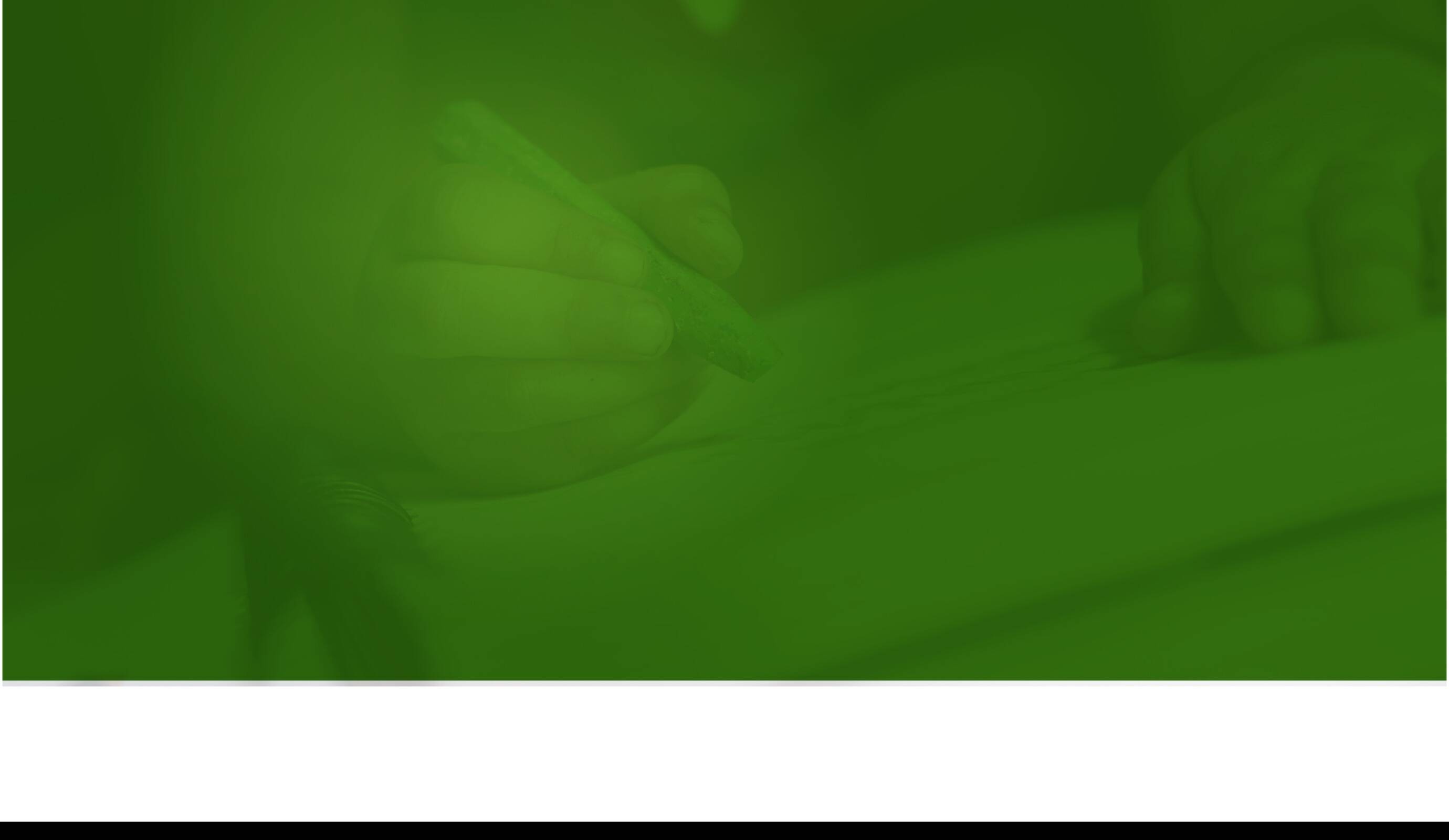
Sustainable solutions
Sustainable solutions 2020 : 103-1, 103-2, 103-3
GRI 416 : 103-1, 103-2, 103-3
Solutions
Back to top


Scroll down
By 2022, we will have significantly reduced the waste of (food) products during storage and transport in our packaging.
Target
LC Packaging Remote Audit Programme
High quality packaging protects the environmental and economic investment in products and contributes to economic development and social well-being by facilitating the distribution and delivery of products to the marketplace. According to the UN, 1.3bn tonnes of food, about a third of all food produced, is wasted each year.
High quality packaging is produced in outstanding production facilities, in a sustainable way, by the best people who work and live under good conditions. To assess these conditions, (potential) customers are regularly invited to visit our production facilities as part of their Quality Assurance programme or as a prerequisite for doing business or implementing new projects. To allow for audit requests in times when travelling is not possible due to the COVID-19 pandemic,
we have put together the LC Packaging Remote Audit Programme. The purpose of this programme is to give an auditor a just-as-good-as-physical audit experience using remote controls, such as documentation and visual impressions, followed by video meetings. An online audit takes a full day and has already resulted in customer approvals. We aim to continue with our Remote Audit Programme after the pandemic.
Valuable products and recourses are lost in various stages throughout the supply chain every day. Only a few types of packaging and production facilities meet the strict food safe and pharma clean requirements. LC Packaging believes that we can actively contribute to preventing the waste of valuable products in supply chains all over the world.
More data in our 2020 Business Ethics Report
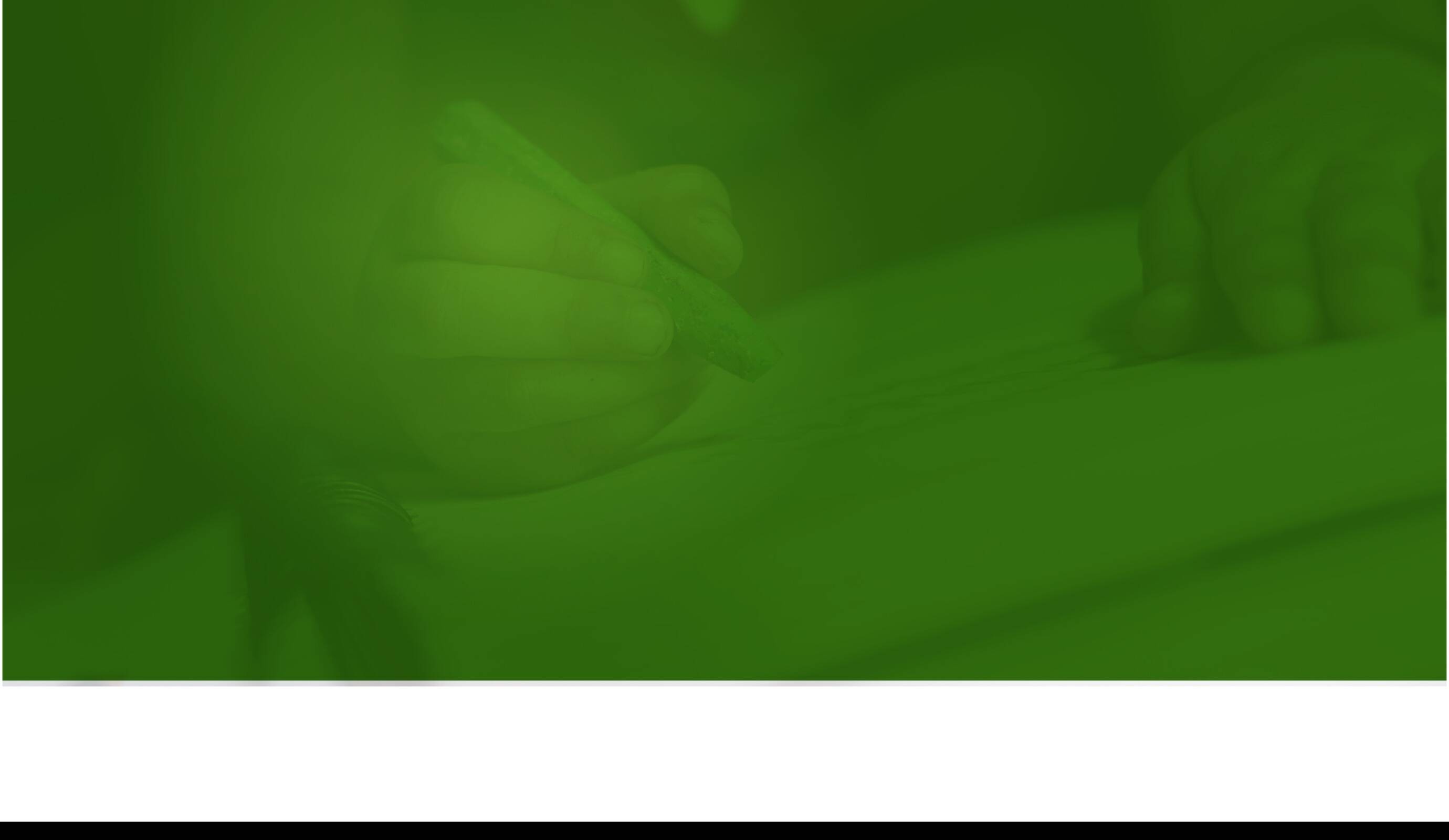
Innovation 2020: 103-1, 103-2, 103-3
Sustainable solutions 2020: 103-1, 103-2, 103-3
Innovations
Solutions
Sustainability is the key element to innovation and optimisation and ideally, should be taken into consideration in every decision or development. This applies to the choices we make regarding our partners, but also our infrastructure, product developments and our circular solutions.
Back to top


Scroll down
By 2022, sustainability will be fully integrated in our innovation processes, leading to sustainable operations and packaging solutions.
Target
After introducing 100% recyclable cardboard sleeves in 2019 as an alternative for plastic wrapping, we have expanded our portfolio in 2020 with punnets especially designed for banding paper, also known as paper bands. Paper bands are sure to hold the product together once packaged and an increasing amount of customers in the fruit and vegetable market are nowadays installing banding paper machinery at their own locations. We have created punnets with flaps, fit for our customer’s machinery, further diminishing the need for plastic wrapping.
In September 2020, LC Packaging International, LC Packaging Netherlands and LC Packaging Global moved into a newly build, state-of-the-art facility that combines office, warehouse and bag printing equipment. The building was built with a strong focus on the well-being of employees, quality and sustainability and has been BREEAM Outstanding certified. This is the ultimate sustainability label for buildings with minimal environmental impact. Innovative measures have been taken to minimise CO2 emissions and the consumption of energy and water. On the roof, 3,032 solar panels have been installed, generating enough energy to supply 386 households for a full year. Rainwater is collected and cleaned using a special roof-membrane and used by nearby horticultural businesses so no water is wasted unnecessarily.
In Pietermaritzburg, South Africa, we are building a new factory for our own production facility LC Shankar. The opportunity to further green our production was one of the main drivers for the build. Besides the use of solar energy, rain water will be harvested for the use of ablution facilities, such as flushing the toilet. Additionally, LC Packaging’s FIBC production facility Dutch-Bangla Pack Ltd. (DBPL) has started construction on its third factory in 2020. The facility provides 4,000 square meters additional floor space and is being built with measures to reduce energy use and water use through extensive insulation and sensors among others.
After use solutions and circularity
We believe plastic packaging is a valuable resource. When sustainably designed, produced, distributed and handled, and with a suitable after-use solution in place, flexible packaging can be re-used, reconditioned and/or recycled and transformed into a high-value next-use application. That is why we focus on establishing a solid after-use infrastructure in partnership with Veolia. Together with a selected group of customers, we are creating and testing a circular programme that focuses on optimising the recovery and upcycling of flexible packaging after-use. To turn used big bags into big bags once more, we have joined forces with Starlinger & Co. GmbH to develop the concept op circular packaging for big bags made from polypropylene fabric. In a laboratory environment, we have been able to create fabric with up to 50% recycled polypropylene granulate (rPP) that can be
used to produce ‘new’ big bags. The big bags with the rPP content show the same quality as big bags made from virgin materials in terms of tensile strength, weight and safety factor. At DBPL), we can produce big bags with 15% rPP of which we have already sold the first batches.
When treated right, big bags can be used up to six times. With our WorldBag reconditioning service, we make a unique contribution to reducing waste streams. WorldBag collects used big bags at our customer’s or their end-user’s location all over Europe, cleaning and repairing them, making them fit for reuse. In 2020, 50,000 big bags were reconditioned by WorldBag. With this closed-loop formula, we offer a unique, efficient, sustainable 100% solution, ensuring the right balance between a long life span and low costs.
Product development
Sustainable infrastructure
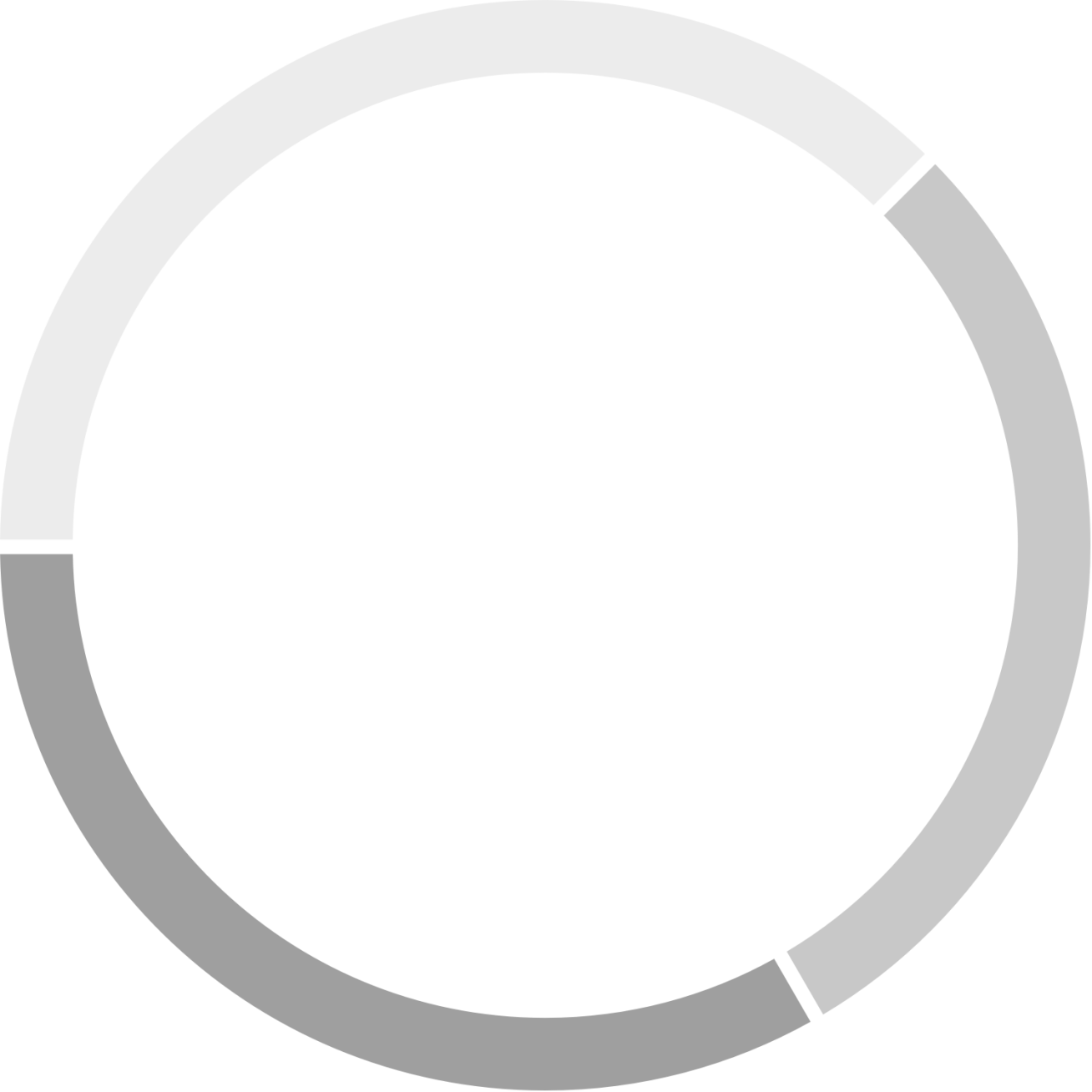
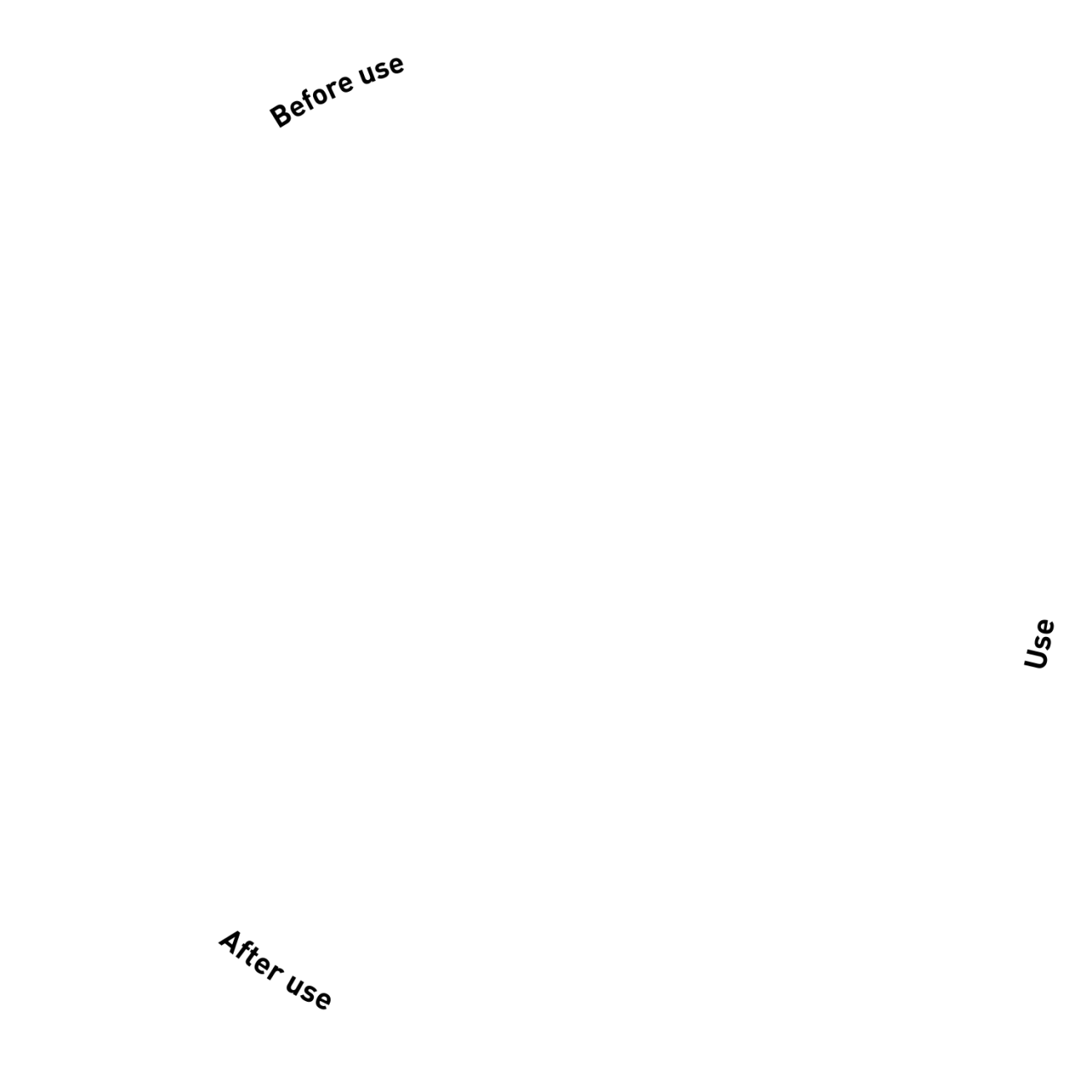
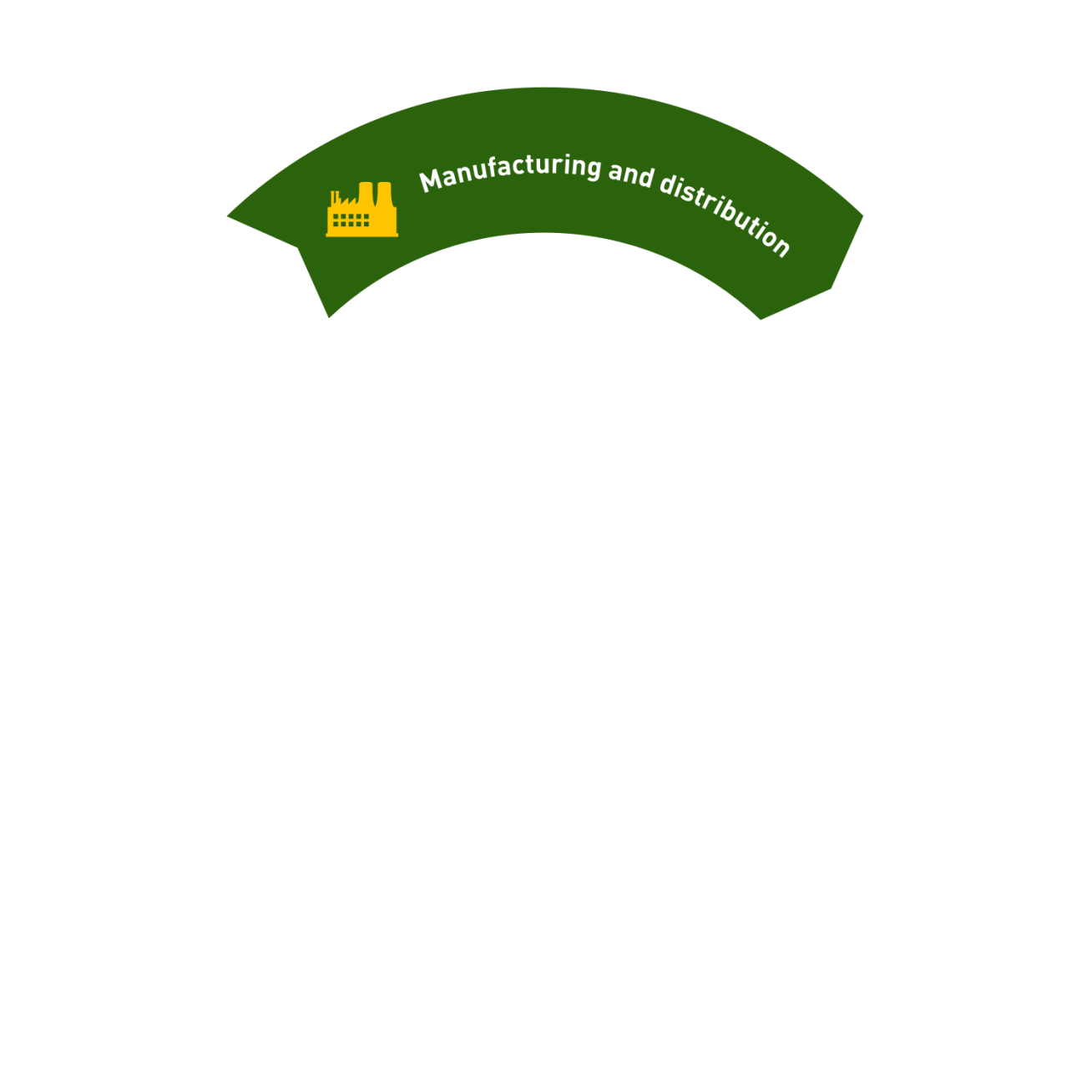
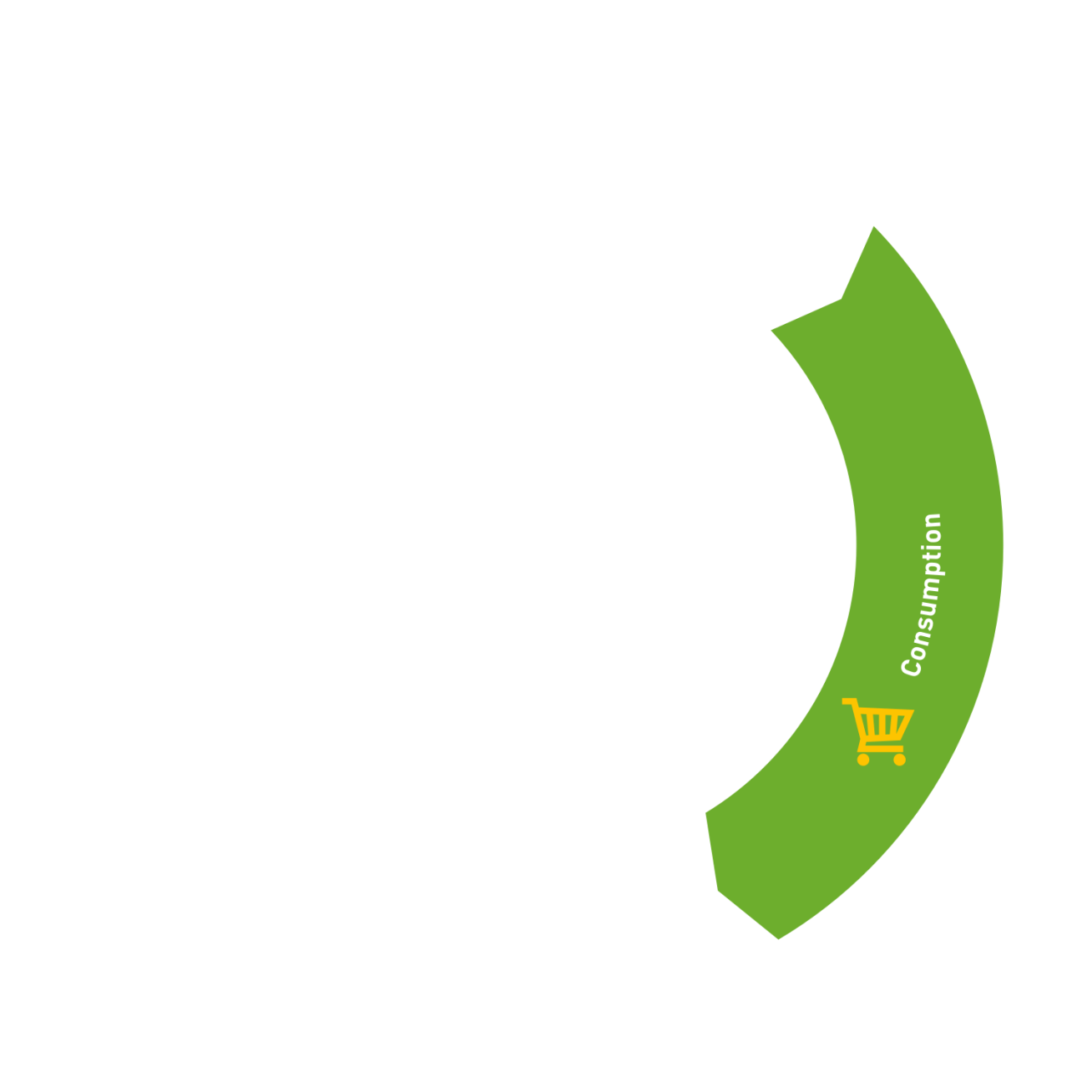
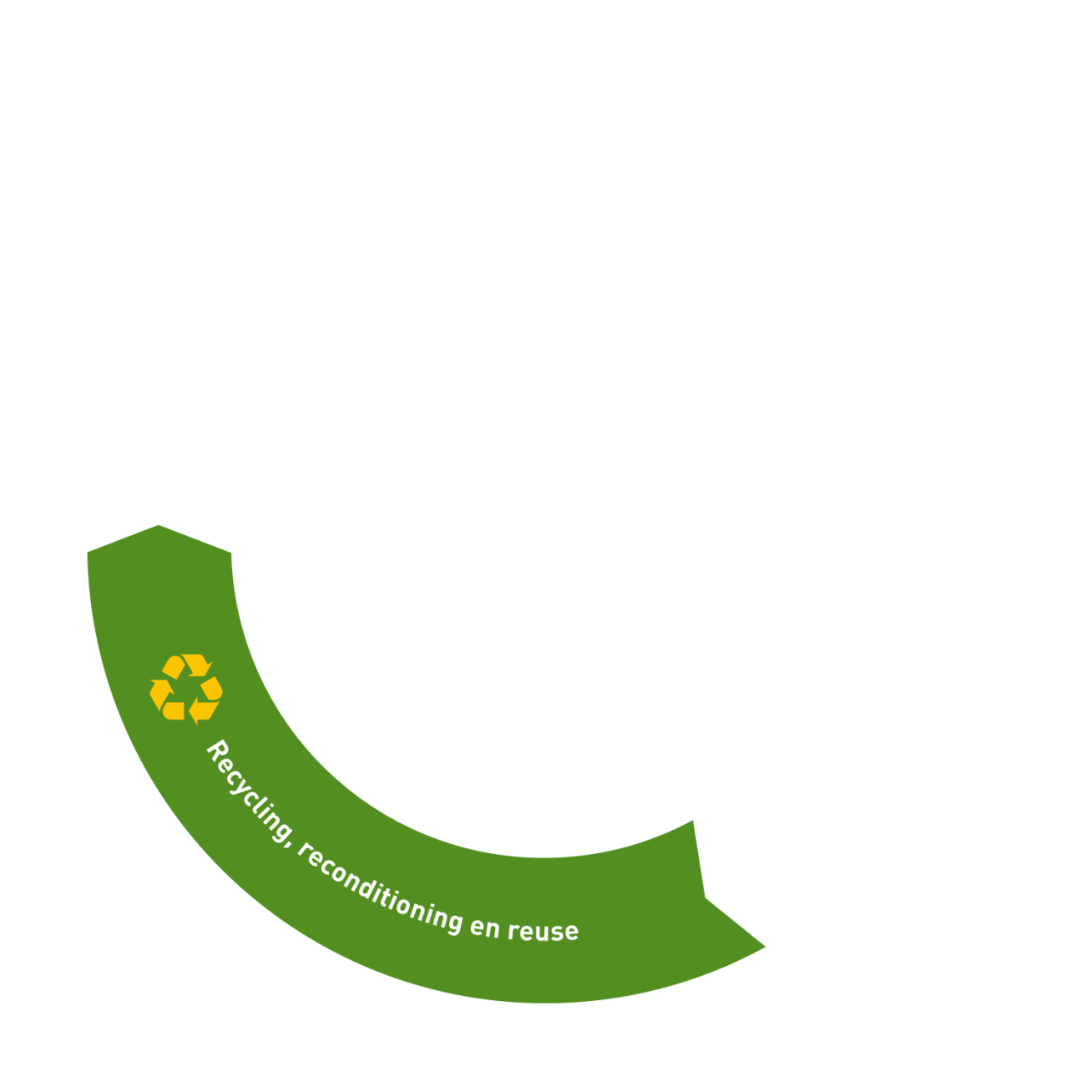
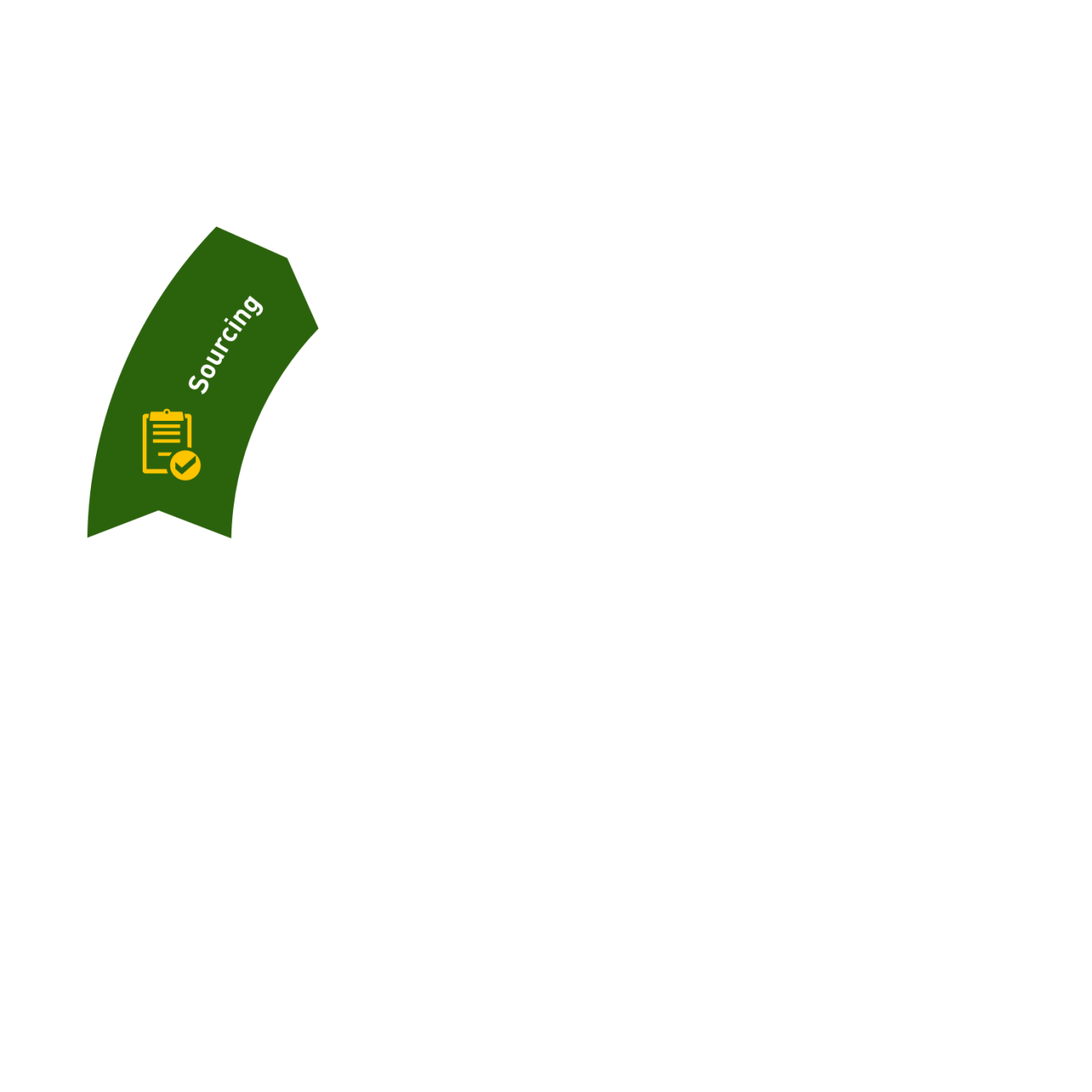

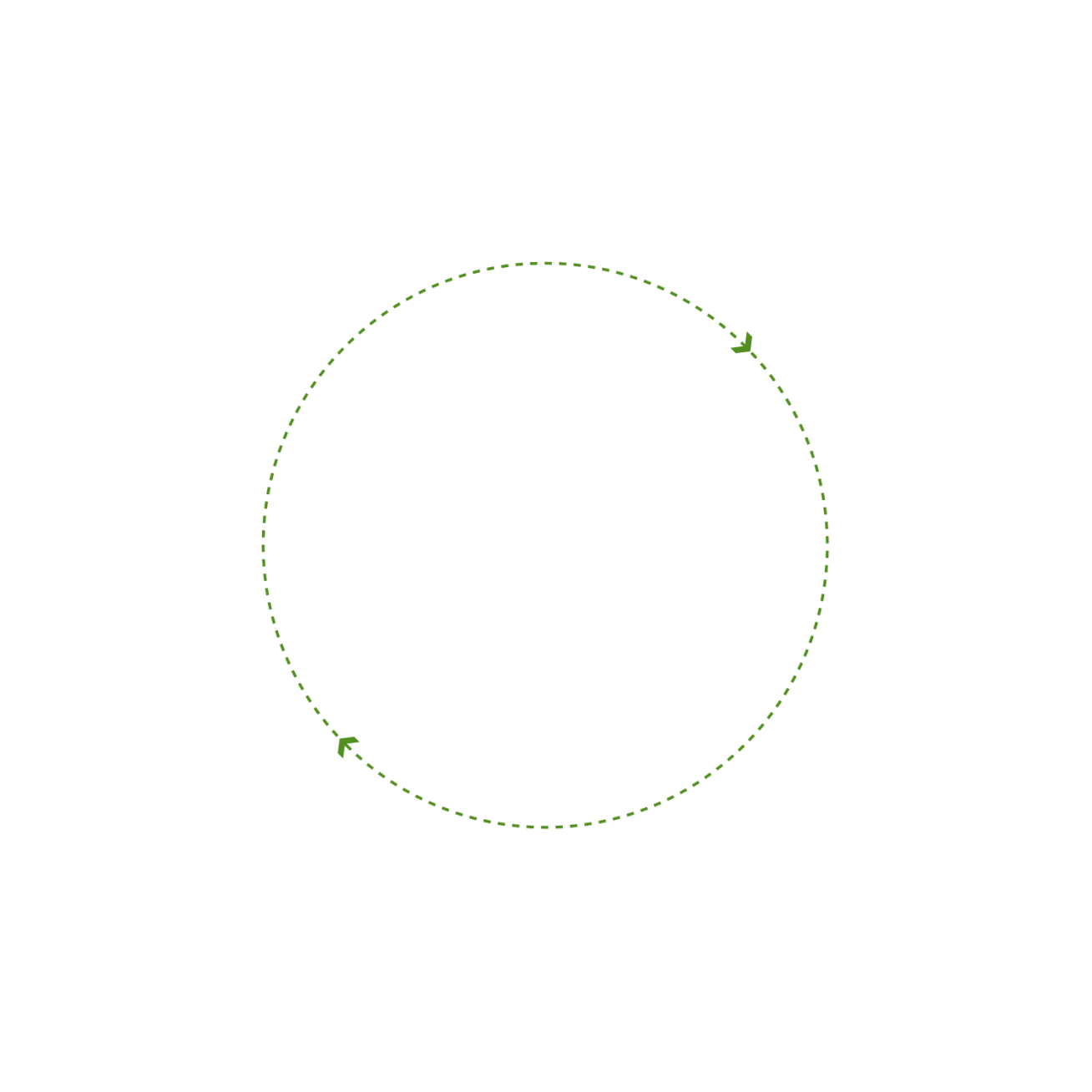
We also continue optimising our plastic packaging. We have decreased the size of our mesh bag labels by half. By reducing the 20 cm labels to 10 cm labels, we have managed to remove 6 gr of plastics per bag. The new label also prevents the packed product from ‘sweating’ behind the label, better preserving the product inside.
More data in our 2020 Solutions Report
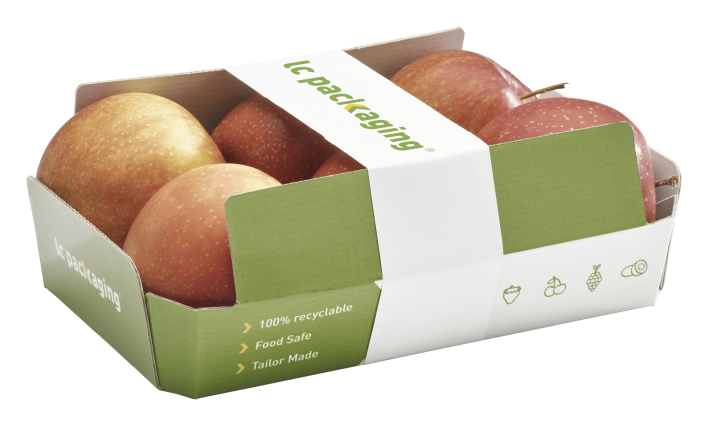
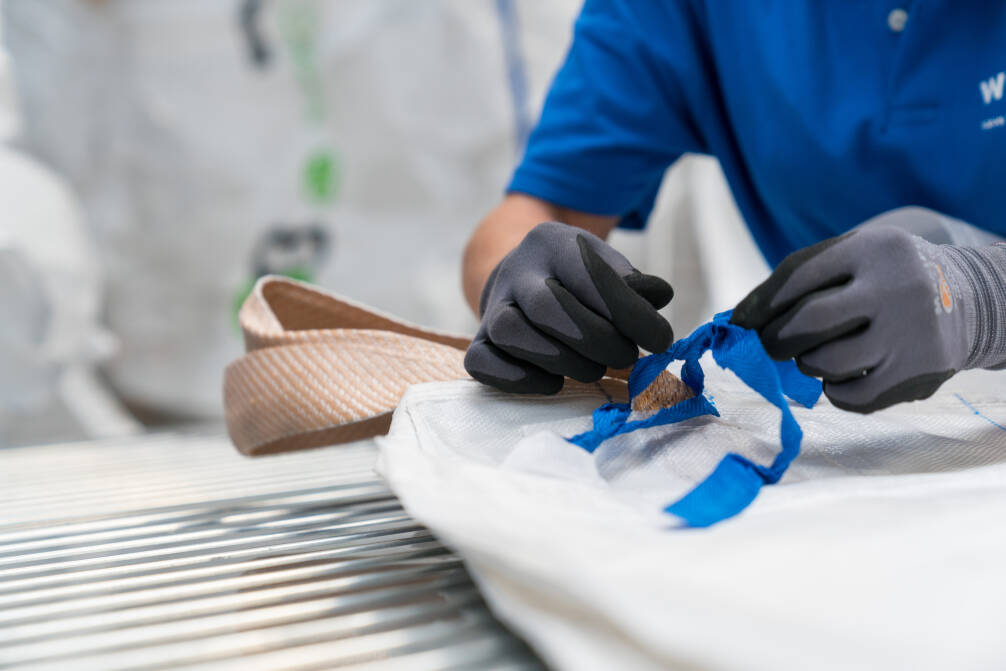
Reusing your big bags does not make them second-hand

Read more
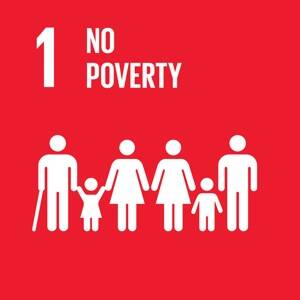
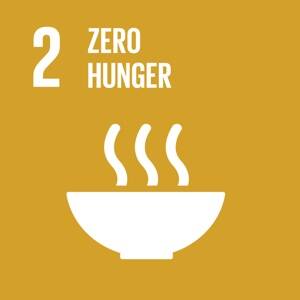
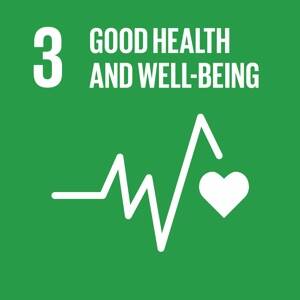
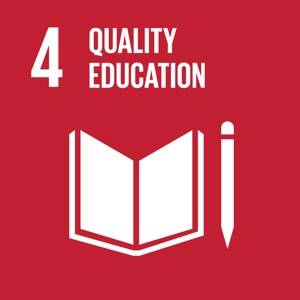
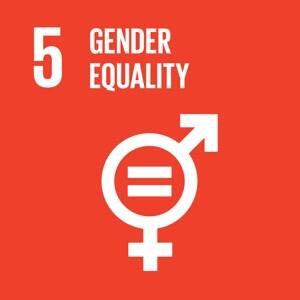
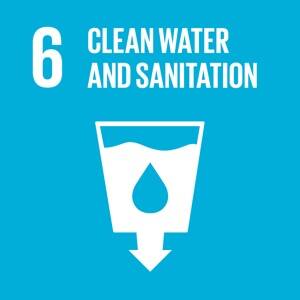
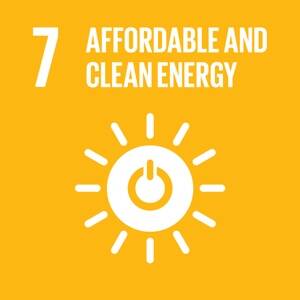
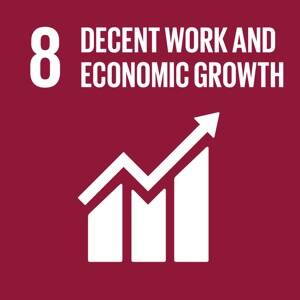
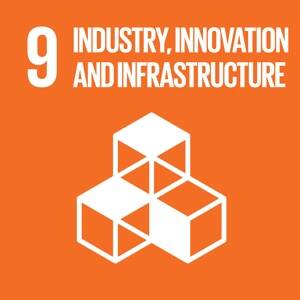
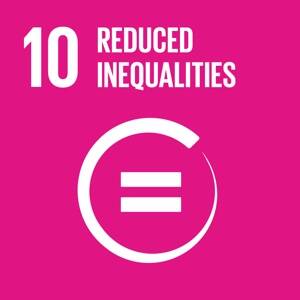
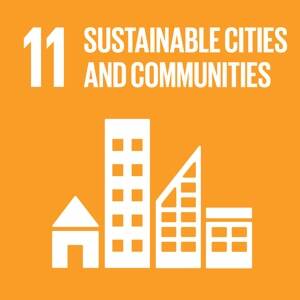
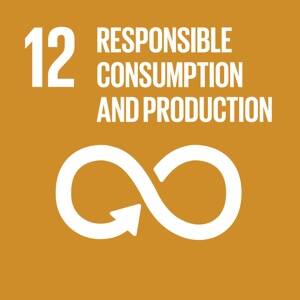
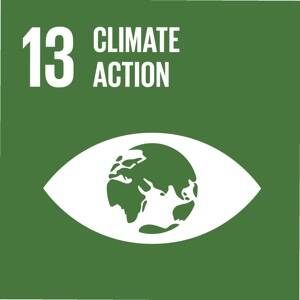
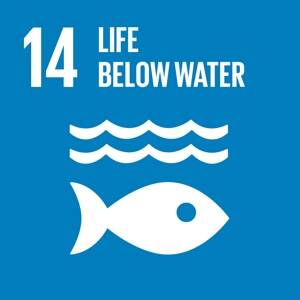
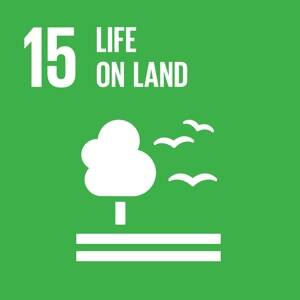
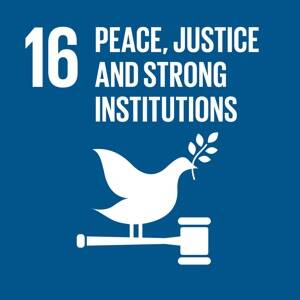
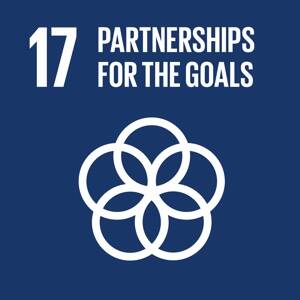
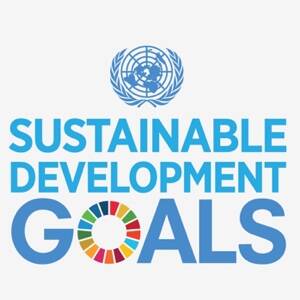
Our contributions
In our daily operations, LC Packaging has a direct impact on Global Sustainable Development Goals (SDGs) 8,9, 12 and 17 as set by the United Nations. However, we are committed and proud to contribute to even more of the SDG's through our actions and initiatives.
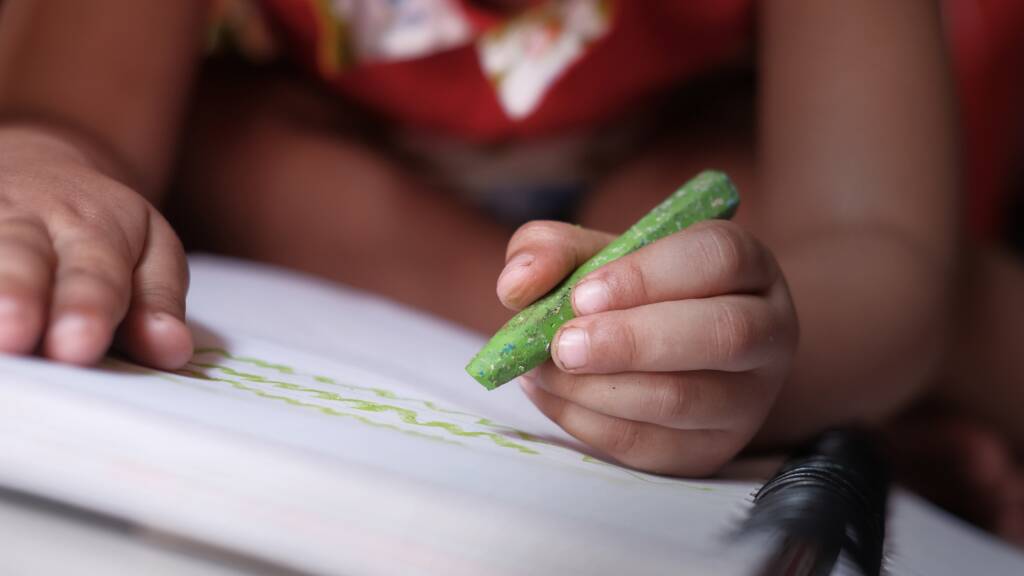
Developing Sustainable packaging Solutions
We are determined to improve the lifecycle of our packaging products one step at the time.
Sustainable materials
Target
By 2022, we will have minimised the waste associated with our packaging.
To minimise the waste related to our packaging, together with our Partners, we analyse, experiment with and optimise:
Materials
LC Packaging products consist of roughly 3 materials: PP/PE (plastics), jute and cardboard. 50% of our packaging solutions is made out of renewable materials and 100% out of recyclable materials. In total, we used approximately 87 million kilos of material for our products in 2020 (88 million in 2019), of which 50% cardboard and 45% PP/PE. Compared to 2019, our use of plastic materials has decreased by 1.3%.
Together with its partners, LC Packaging is actively testing the use of recycled PP (rPP) for the manufacture of new big bags (FIBCs). We have already successfully produced a bag containing 20% rPP from our own PP process waste. Together with our Partner Starlinger, we have produced a 50% rPP bag, including rPP made out of used LC Packaging bags. 39% of the total amount of kgs material used in our packaging are recycled input materials. This compared to 43% in 2019. Our cardboard packaging consists of 85% recycled content.
Recycled content
Our contributions
In our daily operations, LC Packaging has a direct impact on Global Sustainable Development Goals (SDGs) 8,9, 12 and 17 as set by the United Nations. However, we are committed and proud to contribute to even more of the SDG's through our actions and initiatives.
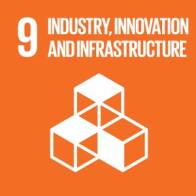
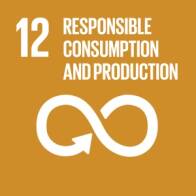
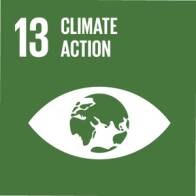
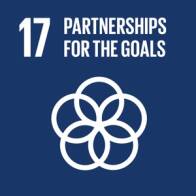
GRI 301: 103-1, 103-2, 103-3
Sustainable solutions 2020: 103-1, 103-2, 103-3
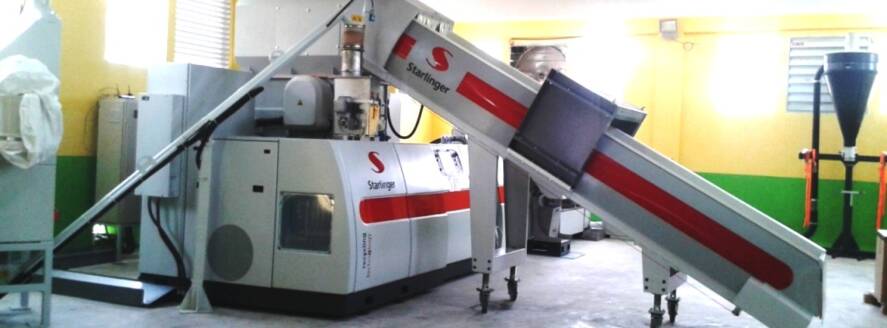
Reusable and recyclable solutions
In 2020, we distributed more than 360 million packaging solutions (337 million in 2019) of which 64% was recyclable. In 2019, we calculated that 98.2% of the packaging distributed was recyclable. In partnership with the Dutch Knowledge Institute for Sustainable Packaging (KIDV), we are in the middle of a deep dive sustainability analysis for all our product groups. Packaging that may theoretically be recyclable, but is difficult to recycle in today’s society, has been identified as non-recyclable in this 2020 report. This explains the decreased percentage of recyclable packaging solutions. The deep dive analysis was conducted to help us define a clear strategy for the upcoming years, with the ultimate goal to make all of our products as circular as possible – starting with 100% recyclable and, where possible, reusable.
Reducing process waste
With our GREENBangla recycling initiative, we once again recycled 80% of our virgin PP process waste in 2020. This adds up to 425 mt. Thanks to a state-of-the-art Starlinger Recycling Machine, 20 high-quality jobs were created for the purpose of upcycling our process waste. In total we recycled 29% of our total global waste production in-house in 2020.
More data in our 2020 Solutions Report.
Our contributions
In our daily operations, LC Packaging has a direct impact on Global Sustainable Development Goals (SDGs) 8,9, 12 and 17 as set by the United Nations. However, we are committed and proud to contribute to even more of the SDG's through our actions and initiatives.
Sustainable solutions
By 2022, we will have significantly reduced the waste of (food) products during storage and transport in our packaging.
Target
High quality packaging protects the environmental and economic investment in products and contributes to economic development and social well-being by facilitating the distribution and delivery of products to the marketplace. According to the UN, 1.3bn tonnes of food, about a third of all food produced, is wasted each year. Valuable products and recourses are lost in various stages throughout the supply chain every day. Only a few types of packaging and production facilities meet the strict food safe and pharma clean requirements. LC Packaging believes that we can actively contribute to preventing the waste of valuable products in supply chains all over the world.
LC Packaging Remote Audit Programme
High quality packaging is produced in outstanding production facilities, in a sustainable way, by the best people who work and live under good conditions. To assess these conditions, (potential) customers are regularly invited to visit our production facilities as part of their Quality Assurance programme or as a prerequisite for doing business or implementing new projects. To allow for audit requests in times when travelling is not possible due to the COVID-19 pandemic, we have put together the LC Packaging Remote Audit Programme. The purpose of this programme is to give an auditor a just-as-good-as-physical audit experience using remote controls, such as documentation and visual impressions, followed by video meetings. An online audit takes a full day and has already resulted in customer approvals. We aim to continue with our Remote Audit Programme after the pandemic.
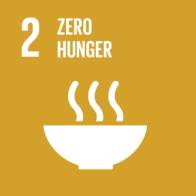
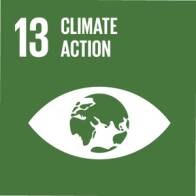
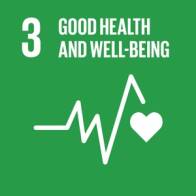
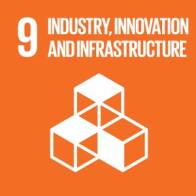
Sustainable solutions 2020 : 103-1, 103-2, 103-3
GRI 416 : 103-1, 103-2, 103-3
More data in our 2020 Business Ethics Report
Innovations
Target
By 2022, sustainability will be fully integrated in our innovation processes, leading to sustainable operations and packaging solutions.
Sustainability is the key element to innovation and optimisation and ideally, should be taken into consideration in every decision or development. This applies to the choices we make regarding our partners, but also our infrastructure, product developments and our circular solutions.
Product development
After introducing 100% recyclable cardboard sleeves in 2019 as an alternative for plastic wrapping, we have expanded our portfolio in 2020 with punnets especially designed for banding paper, also known as paper bands. Paper bands are sure to hold the product together once packaged and an increasing amount of customers in the fruit and vegetable market are nowadays installing banding paper machinery at their own locations. We have created punnets with flaps, fit for our customer’s machinery, further diminishing the need for plastic wrapping.
We also continue optimising our plastic packaging. We have decreased the size of our mesh bag labels by half. By reducing the 20 cm labels to 10 cm labels, we have managed to remove 6 gr of plastics per bag. The new label also prevents the packed product from ‘sweating’ behind the label, better preserving the product inside.
Sustainable infrastructure
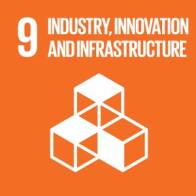
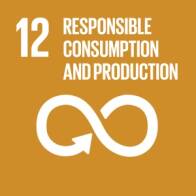
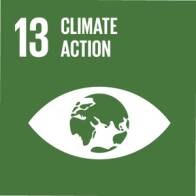
Our contributions
In our daily operations, LC Packaging has a direct impact on Global Sustainable Development Goals (SDGs) 8,9, 12 and 17 as set by the United Nations. However, we are committed and proud to contribute to even more of the SDG's through our actions and initiatives.
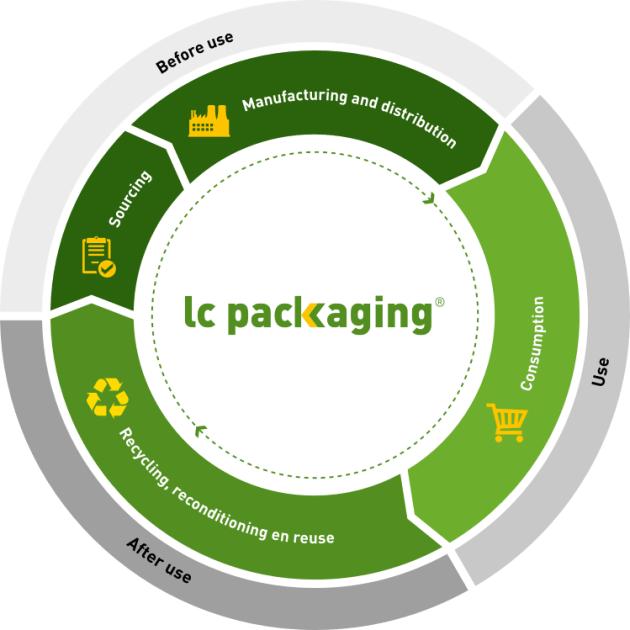
Innovation 2020: 103-1, 103-2, 103-3
Sustainable solutions 2020: 103-1, 103-2, 103-3
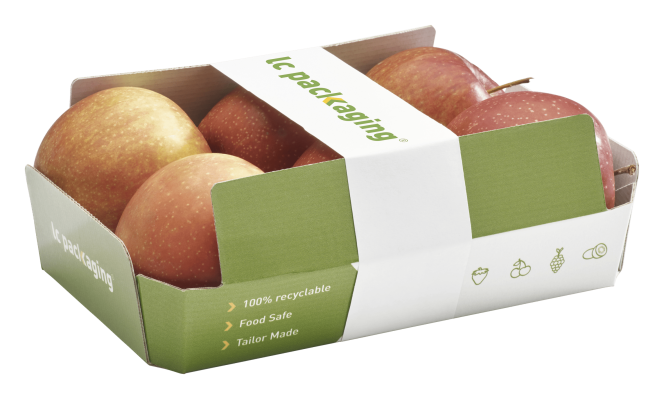
After use solutions and circularity
More data in our 2020 Solutions Report
In September 2020, LC Packaging International, LC Packaging Netherlands and LC Packaging Global moved into a newly build, state-of-the-art facility that combines office, warehouse and bag printing equipment. The building was built with a strong focus on the well-being of employees, quality and sustainability and has been BREEAM Outstanding certified. This is the ultimate sustainability label for buildings with minimal environmental impact. Innovative measures have been taken to minimise CO2 emissions and the consumption of energy and water. On the roof, 3,032 solar panels have been installed, generating enough energy to supply 386 households for a full year. Rainwater is collected and cleaned using a special roof-membrane and used by nearby horticultural businesses so no water is wasted unnecessarily.
In Pietermaritzburg, South Africa, we are building a new factory for our own production facility LC Shankar. The opportunity to further green our production was one of the main drivers for the build. Besides the use of solar energy, rain water will be harvested for the use of ablution facilities, such as flushing the toilet. Additionally, LC Packaging’s FIBC production facility Dutch-Bangla Pack Ltd. (DBPL) has started construction on its third factory in 2020. The facility provides 4,000 square meters additional floor space and is being built with measures to reduce energy use and water use through extensive insulation and sensors among others.
We believe plastic packaging is a valuable resource. When sustainably designed, produced, distributed and handled, and with a suitable after-use solution in place, flexible packaging can be re-used, reconditioned and/or recycled and transformed into a high-value next-use application. That is why we focus on establishing a solid after-use infrastructure in partnership with Veolia. Together with a selected group of customers, we are creating and testing a circular programme that focuses on optimising the recovery and upcycling of flexible packaging after-use. To turn used big bags into big bags once more, we have joined forces with Starlinger & Co. GmbH to develop the concept op circular packaging for big bags made from polypropylene fabric. In a laboratory environment, we have been able to create fabric with up to 50% recycled polypropylene granulate (rPP) that can be used to produce ‘new’ big bags. The big bags with the rPP content show the same quality as big bags made from virgin materials in terms of tensile strength, weight and safety factor. At DBPL), we can produce big bags with 15% rPP of which we have already sold the first batches.
When treated right, big bags can be used up to six times. With our WorldBag reconditioning service, we make a unique contribution to reducing waste streams. WorldBag collects used big bags at our customer’s or their end-user’s location all over Europe, cleaning and repairing them, making them fit for reuse. In 2020, 50,000 big bags were reconditioned by WorldBag. With this closed-loop formula, we offer a unique, efficient, sustainable 100% solution, ensuring the right balance between a long life span and low costs.

Reusing your big bags does not make them second-hand

Read more