Sustainable materials
We are determined to improve the lifecycle of our packaging products one step at the time.
Developing sustainable
packaging solutions
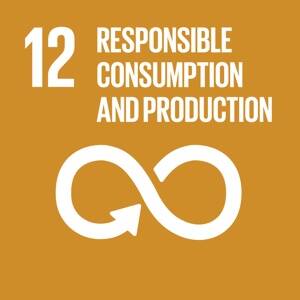
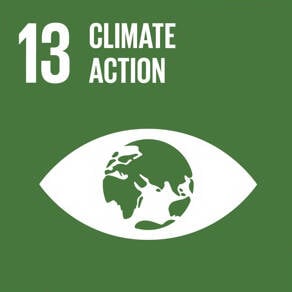
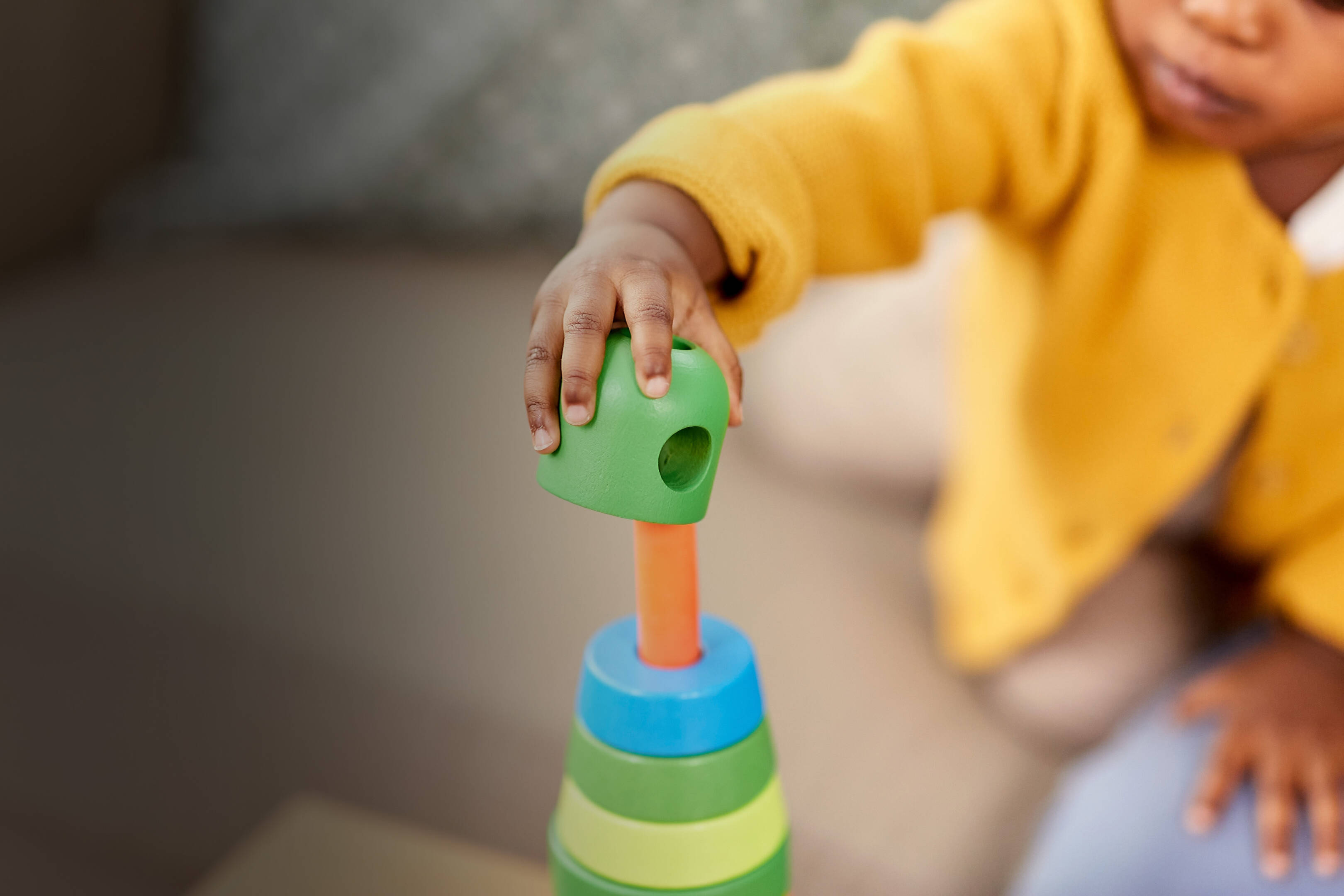
We have set ourselves 3 very ambitious and measurable goals for 2030 in which innovation and optimisation are key factors for success. By 2030, 80% of our revenue should come from products that deliver the circular economy, and we aim to have achieved a 50% emissions reduction from our value chain. Soon, we will expand our Research & Development activities by bringing missing knowledge in-house, and by seeking out new partnerships and external initiatives. Read more about our future ambitions in our 2030 Ambition magazine.
Initiatives and actions
Below we have summarised a selection of our initiatives to reduce the waste related to our packaging:
- Together with the Netherlands Institute for Sustainable Packaging (KIDV) we have performed a deep-dive sustainability analysis of our packaging portfolio and determined next steps towards delivering a circular economy.
- We have joined the Prevent Waste Alliance and the Plastic Pact Netherlands, thereby committing to help accelerate the transition to a circular economy: to do more with less plastic.
- To reduce the use of materials in our packaging, we have decreased the weight of our net bags with 3%-5%, saving approx. 40,000 KG of materials annually.
- We encourage the reuse of FIBCs with the help of our Worldbag reconditioning service, saving up to 10 KG of material per bag, when using the bag 5 times.
- Together with our customer Nestlé Portugal we have set up an on-site reuse project to significantly decrease the amount of plastic waste in its operations. The value of the project was recognised with the Nestlé Sustainability Award for Suppliers 2021.
- We have joined forces with colleagues in the industry in a working group organised by EFIBCA and EuroJute, to launch an Industry Design for Recycling (DfR) Standard for FIBCs. The DfR standard is expected to be taken into use in Q3 of 2022.
- To increase recyclability, we designed a Woven PP bag together with one of our valued customers, which is made of 98% polypropylene.
- With WPP bags that provide maximum stability during transport for one of our customers in the malt industry, we were able to reduce plastic use by 45% as extra hooder material was eliminated from the process.
- In 2019, we introduced 100% recyclable cardboard sleeves as an alternative to plastic wrapping.
- Our own production facility Dutch-Bangla Pack ltd. and our key production partners are now able to produce FIBCs with 30% recycled content. This has been achieved without having to increase the weight of the fabric, and the FIBCs remain as strong and safe as a bag from virgin material.
- To reduce process waste, in 2017, together with local partners, we initiated a first-of-its kind waste recycling project: GreenBangla. In 2021 we have recycled 503,606 KG through this GreenBangla initiative;
- We have teamed up with Veolia to minimise waste related to flexible packaging.
- Together with Starlinger & Co. GmbH we closed the loop on FIBCs by turning big bags into big bags once more for the first time. We also work together with Healix on producing high-quality rPP made from Post Consumer Recycling (PCR) materials.
- Together with our customer M.B. Nieuwenhuijse we have introduced plastic neutral bags.
Initiatives and actions
Measuring progress
Back in 2017, we decided success is to be measured by the outcomes of research on the total KGs of material use and waste produced in our operations in 2017 and 2022.
The two factors and measuring their success, and the fact that the goals itself is not measurably formulated, make it difficult to formulate just one outcome as a result for this goal.
- Since 2016, we have seen an annual increase in turnover. Since 2019, we annually report on the number of distributed packaging products, which has increased by 6% per year on average to 382 million products in 2021. The number of packaging products reused with the help of our in-house WorldBag reconditioning service has remained roughly the same over the past years. Based on these data, we assume that the total number of kilograms of materials used for our packaging has increased compared to baseline year 2016.
- This year we reported a decrease of the total KGs of materials used in our packaging of 18% since 2019 (first year of reporting). However, as our reporting data has become more accurate in 2021 and as some of the calculations made are still based on rough calculations, we choose not to draw conclusion from this.
- Compared to 2016 we have reduced the waste produced in our own operations with 72%. Over 38% of our waste is recycled with the help of our in-house waste recycling initiative GreenBangla, recycling up to 80% of our process waste at our FIBC production facility in Bangladesh.
- Additionally, in the past years we learned that there are many more elements impacting the waste related to our packaging, such as the reusability and recyclability of our packaging and the use of recycled content materials. Especially in these areas, we have made important steps and achievements.
Outcome
Baseline
Back in 2017, together with our production partners we were in the early stages of analysing existing packaging solutions on the type of materials used and the amount of waste related to these solutions in order to come up with more sustainable packaging.
achieved
100%
Target
By 2022, we will have minimised the waste associated with our packaging.
Scroll down


Back to top
To minimise the waste related to our packaging, together with our Partners, we analyse, experiment with and optimise:
Solutions
Sustainable materials
GRI 301: 103-1, 103-2, 103-3
Sustainable solutions 2021: 103-1, 103-2, 103-3
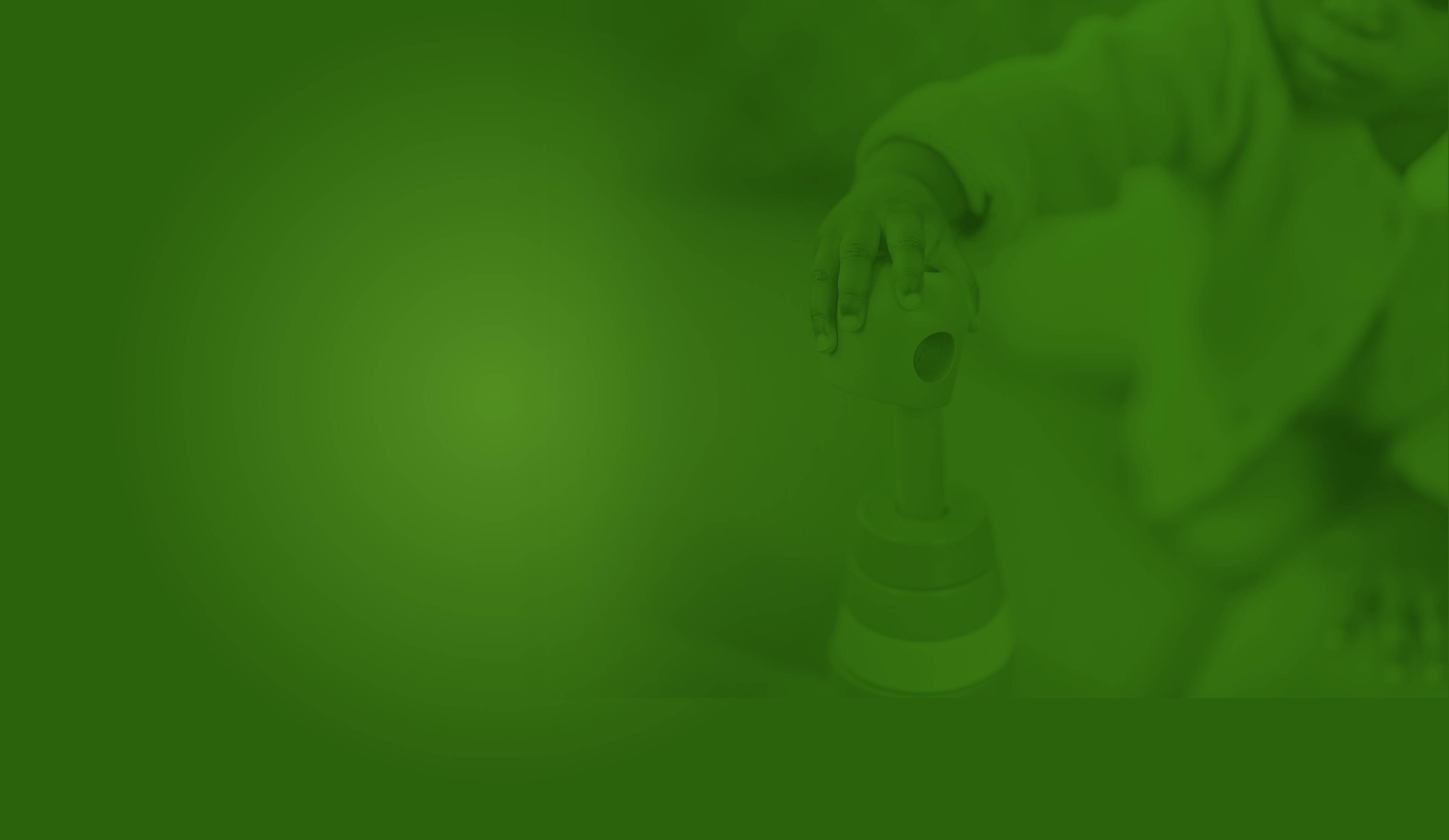
Back in 2017, we were already working on several initiatives to prevent the waste of products during storage and transportation, such as, for example, the ventilated big bag, that allows its cargo, like potatoes or wood logs, to breath and prevents contamination. Also, we provided special bags for transport, and storage, for example, safe and clean food packaging to safely transport milk powder.
Quality packaging protects the environmental, social, and economic investment in products and contributes to economic development and social well-being by facilitating the distribution and delivery of products to the marketplace in pristine condition.
Measuring progress
Success is measured by the intensity and success of our sustainable packaging solutions to prevent the waste of products during storage and/or transportation.
We have summarised a selection of our initiatives and actions to go above and beyond in protecting valuable goods from going to waste:
- Together with our customers we identify ‘product waste’ issues and new opportunities.
- All our packaging is tailor-made to suit the products’ properties and circumstances of transport and fits customer processes and technical demands.
- We have expanded our dedicated international in-house Quality department and have established a team of local quality managers to ensure our packaging is always manufactured according to the highest standards and passes the most stringent tests.
- We have installed ultramodern in-house testing facilities and have invested in cutting-edge technologies and clean room facilities.
- A centrally controlled quality management system (QMS) was implemented.
- To ensure quality even in times when travelling is not possible due to the COVID-19 pandemic, in 2020 we have put together a Remote Audit Programme, using remote controls, such as documentation and visual impressions, followed by video meetings.
- We score 8/10 on sustainable procurement and a 9/10 on Labour and Human Right in our 2021 EcoVadis Assessment, far above the industry average. Responsible sourcing and production, and good working conditions highly minimises the risk of quality issues and mistakes.
- Back in 2017, we have launched our Food Safe and Pharma Clean Assurance Programmes, offering the cleanest and safest packaging that meets the highest industry standards and is produced in our own state-of-the-art cleanroom facilities.
- In 2019, multiple top 5 players in the dairy industry among others, audited and approved our newly built 4,000 m2 state-of-the-art cleanroom with a 100% score for the manufacturing of high-care food.
- Our optimised Food safe and Pharma clean big bags and clean-room big bags meet all standards for clean packaging and are hygienic, odourless and minimise the risk of antistatic discharges.
- Literally a breath of fresh air! Protective, but flexible and breathable packaging, such as net bags, and our ventilated big bag, prevent for example onions and seed potato from sweating and rotting in transit; all developed in-house.
- Our technical textiles protect crops from animals and adverse weather conditions.
- For products such as powders and granulates, the form-stable QBag was designed protecting products from any leaks during filling, storage, transport and discharge.
- WPP bags – in which we are a global leader - with a block bottom also provide better filling properties and a stand-up capacity.
- To protect products against oxygen, water vapor and UV, our big bags and WPP bags can be fitted with a protective inner liner.
- Shelf ready packaging reduces the risk of valuable products as it eliminates a whole packaging cycle. This type of packaging serves as transport packaging, and when arrived at the marketplace it can be placed directly on the shelves of the store.
We aim to continue to excel in our core business of deliver safe and reliable (transport) packaging for dry bulk goods with sustainability at the top of our agenda.
Initiatives and actions
Outcome
Looking back, this goal should not be a goal, because this is what we do at the core of our business: protect valuable goods from going to waste during its journey through the supply chain. Furthermore, this target was unclearly formulated and is therefore not directly measurable. We have therefore decided to measure the achievement of this goal by the number of developments that have taken place to protect the products we package even better: our efforts to go above and beyond.
Baseline
achieved
100%
Target
By 2022, we will have significantly reduced the waste of (food) products during storage and transport in our packaging.
Scroll down


Back to top
Solutions
Sustainable solutions 2021 : 103-1, 103-2, 103-3
GRI 416 : 103-1, 103-2, 103-3
Sustainable solutions
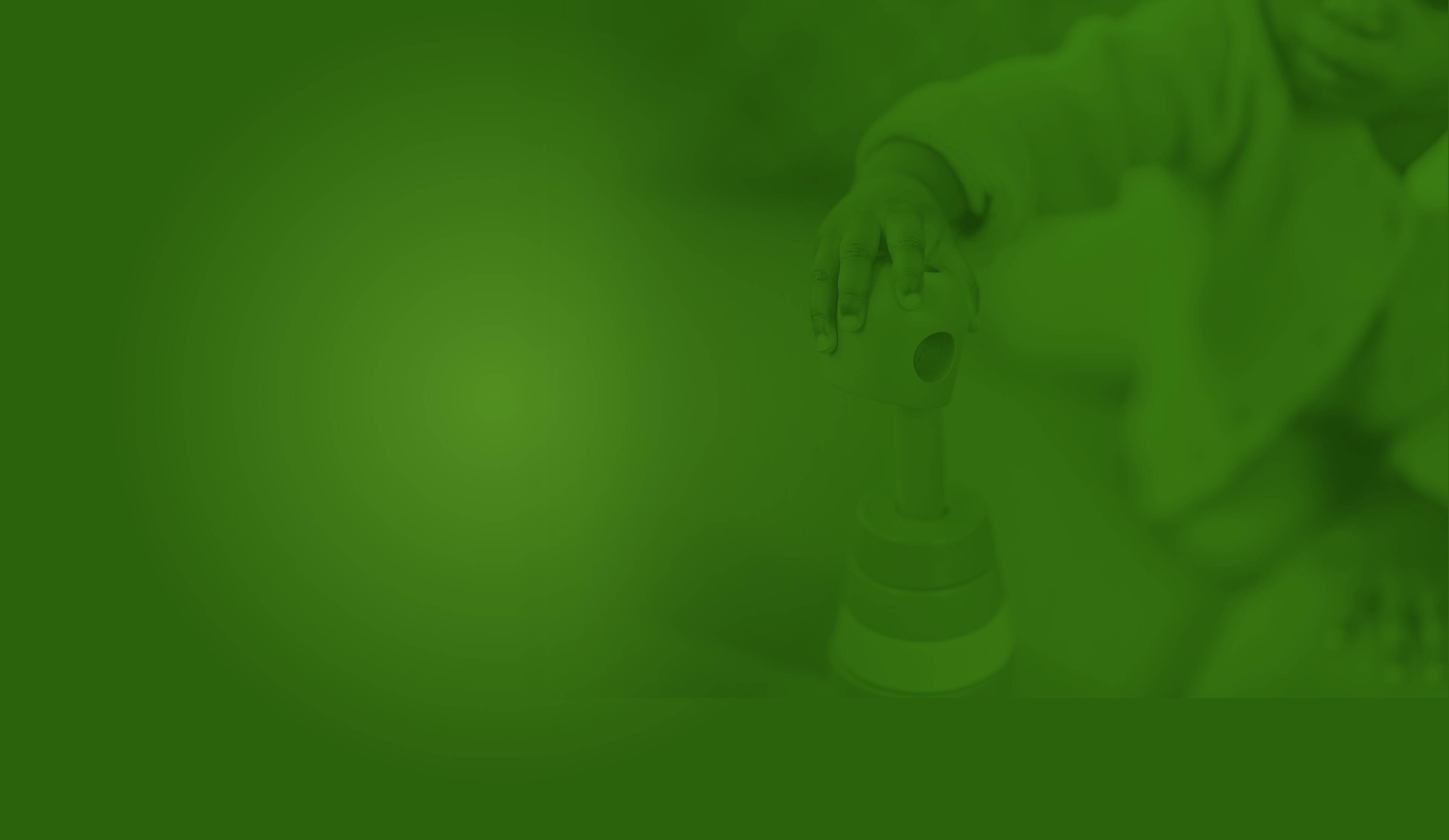
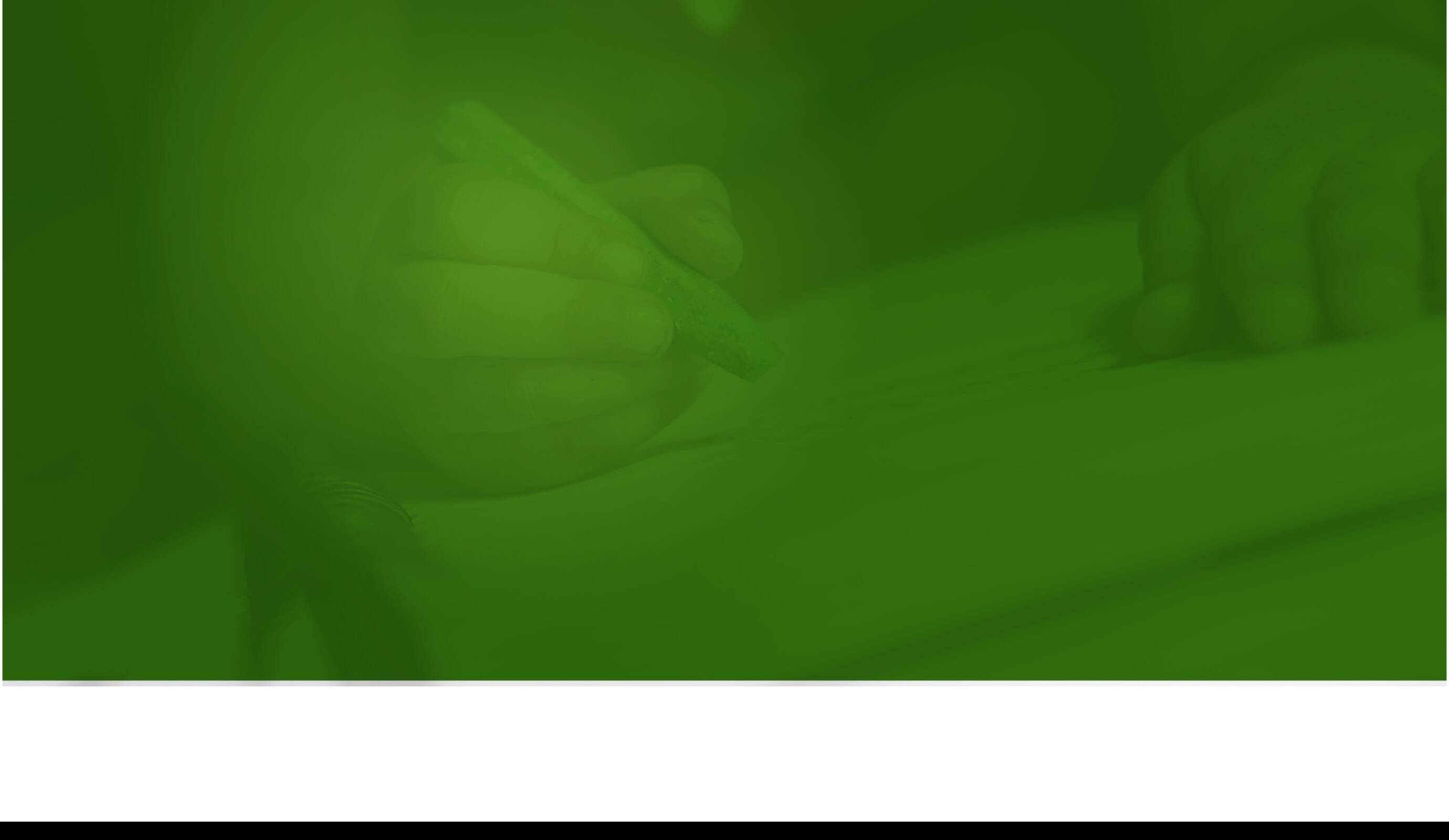
Future ambitions
We have set ourselves 3 very ambitious and measurable goals for 2030 in which innovation and optimisation are key factors for success. By 2030, 80% of our revenue should come from products that deliver the circular economy, and we aim to have achieved a 50% emissions reduction from our value chain. These goals can only be achieved when sustainability, in addition to quality, plays a leading role in all our innovation activities, and when innovation itself becomes a top priority on our corporate agenda. When we do so we can, for example, create our circular packaging portfolio, make production processes more sustainable, and optimise and innovate our activities and services. Soon, we will expand our Research & Development activities by bringing missing knowledge in-house, and by seeking out new partnerships and external initiatives. Read more about our future ambitions in our 2030 Ambition magazine.
More data in our 2021 Solutions Report
Outcome
Baseline
A selection of our innovative initiatives and actions for more sustainable operations and packaging solutions:
- In 2017, together with local partners, we initiated a first-of-its kind waste recycling project: GreenBangla. The initiative was recognised by the UN Global Compact Network Netherlands in their SDG Progress Report 2018 ‘Companies on the way to 2030’. In 2021 we have recycled 503,606 KG through the GreenBangla initaitive.
- To increase recyclability, we designed a Woven PP bag together with one of our valued customers, which is made of 98% polypropylene.
- To reduce our CO2 footprint in 2018, we focused on more sustainable container loading solutions together with our production partners. By making small adjustments to PP bags, we created 6% more container capacity, and by pressing Leno bag bales tighter, we created up to 20% more loading capacity; saving 25 containers being shipped per year.
- In 2019, we introduced 100% recyclable cardboard sleeves as an alternative to plastic wrapping.
- With WPP bags that provide maximum stability during transport for one of our customers in the malt industry, reducing plastic use by 45% as extra hooder material was eliminated from the process.
- In 2020 we launched our HSI (How Sustainable Is…) Programme to identify key components for a sustainable future for our packaging solutions, resulting in a short-term and long-term road map for R&D to make our packaging deliver the circular economy.
- Our own production facility Dutch-Bangla Pack ltd. and our key production partners are now able to produce FIBCs with 30% recycled content. This has been achieved without having to increase the weight of the fabric, and the FIBCs remain as strong and safe as a bag from virgin material.
- Together with our customer Nestlé Portugal we have set up an on-site reuse project to significantly decrease the amount of plastic waste in its operations. The value of the project was recognised with the Nestlé Sustainability Award for Suppliers 2021.
- Our LC Ireland branch partnered with Marlet Property Group for the development of a high-quality, innovative, and environmentally sound solution for waste management in residential areas.
- We have invested in greening our production through energy efficient machinery, sustainable building materials, LED lighting, and electric vehicles among others. Read more about our sustainable production.
- Additionally, several LC Packaging warehouses have replaced their machinery with new printers that will not only offer higher quality prints, but also enable us to switch from solvent-based ink for polypropylene bags to water-based ink.
- In 2020 we finished the build of our new, BREEAM Outstanding certified Head Office that was build with sustainability in mind, contributing to the environment in a positive way.
Initiatives and actions
Our success is measured by two factors: 1) the number of initiatives/projects in which sustainability was a key factor, and 2) the percentage of turnover coming from sustainable packaging solutions.
Measuring success
Although sustainability was an important topic on our agenda back in 2017, we did not yet fully integrate this topic into our innovation processes and decision making.
The two factors and measuring their success make the result for this goal difficult to formulate just one outcome. Looking at the number of initiatives and projects deployed over the past five years; we have innovated and optimised our products, infrastructure, and services, and we have started partnerships to reach our goals, which have led to innovative solutions. In all initiatives and projects, sustainability is a key factor in the decision-making process.
The second metric of measuring success that we had identified back in 2017 was the percentage of turnover coming from sustainable packaging solutions. For this, our baseline year ultimately became 2019, as this was the first year. We measured the percentage of turnover coming from recyclable packaging (83%), which we at that time identified as ‘sustainable packaging’. As throughout the years, we evolved the definition for recyclable packaging twice – in 2020 based on input through our partnership with Veolia and in 2021 based on a deep-dive analysis of our packaging portfolio in cooperation with the Netherlands Institute for Sustainable Packaging (KIDV) - the metric was measured based on different standards over the years and therefore not suitable to measure the results of this goal.
In 2022, we have adopted the definition for sustainable packaging as defined by the Sustainable Packaging Coalition (SPC), based on 8 criteria for sustainable packaging.
achieved
100%
Target
By 2022, sustainability will be fully integrated in our innovation processes, leading to sustainable operations and packaging solutions.
Scroll down


Back to top
We believe optimisation and innovation is key for the future of our company, our employees, our partners, and our customers. We focus on improving infrastructure and our operations and creating innovative packaging solutions that support our customers as they seek to meet the needs of their consumers, while also reducing the impact on the environment.
Solutions
Innovations
Innovation 2021: 103-1, 103-2, 103-3
Sustainable solutions 2020: 103-1, 103-2, 103-3
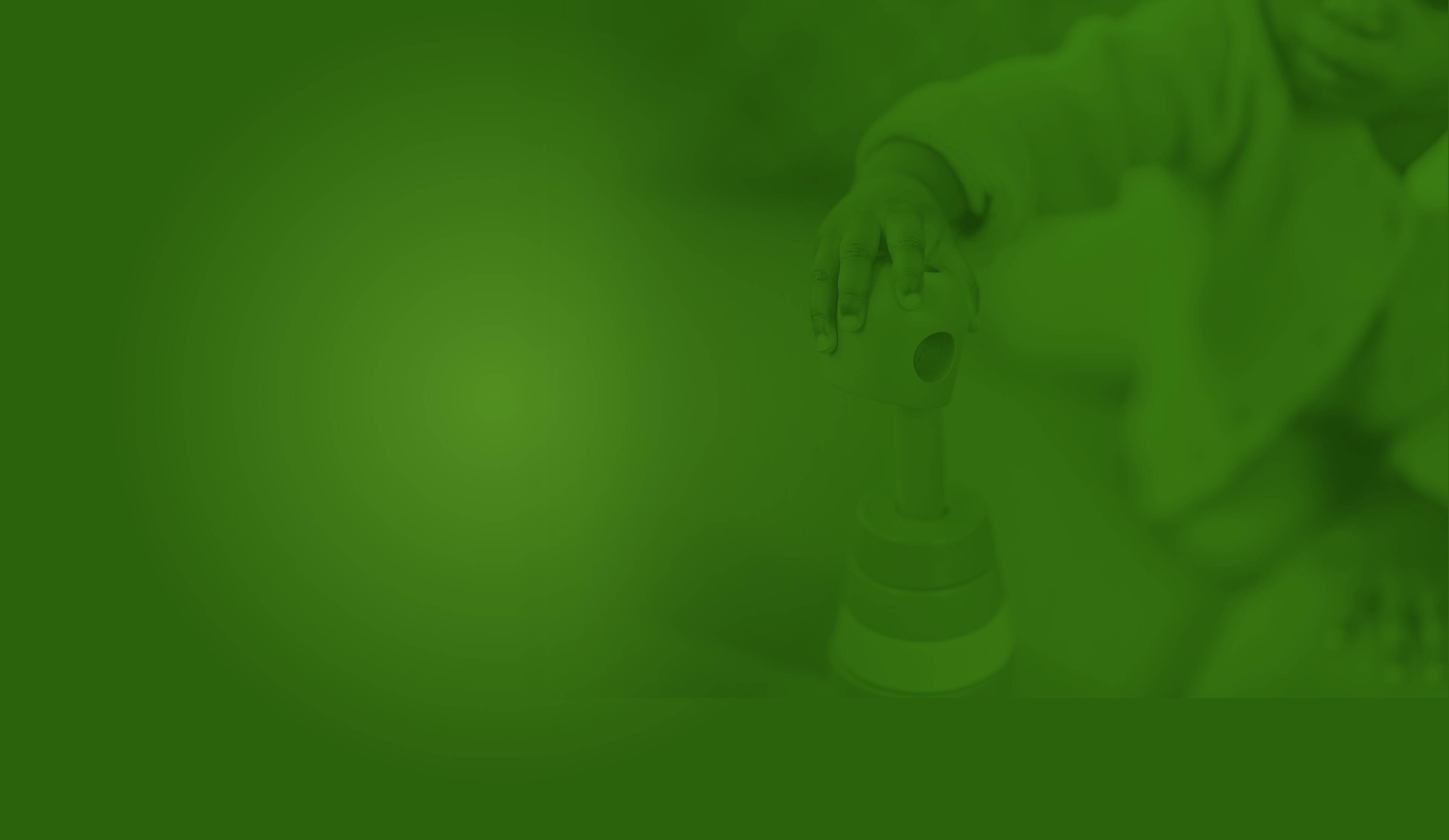
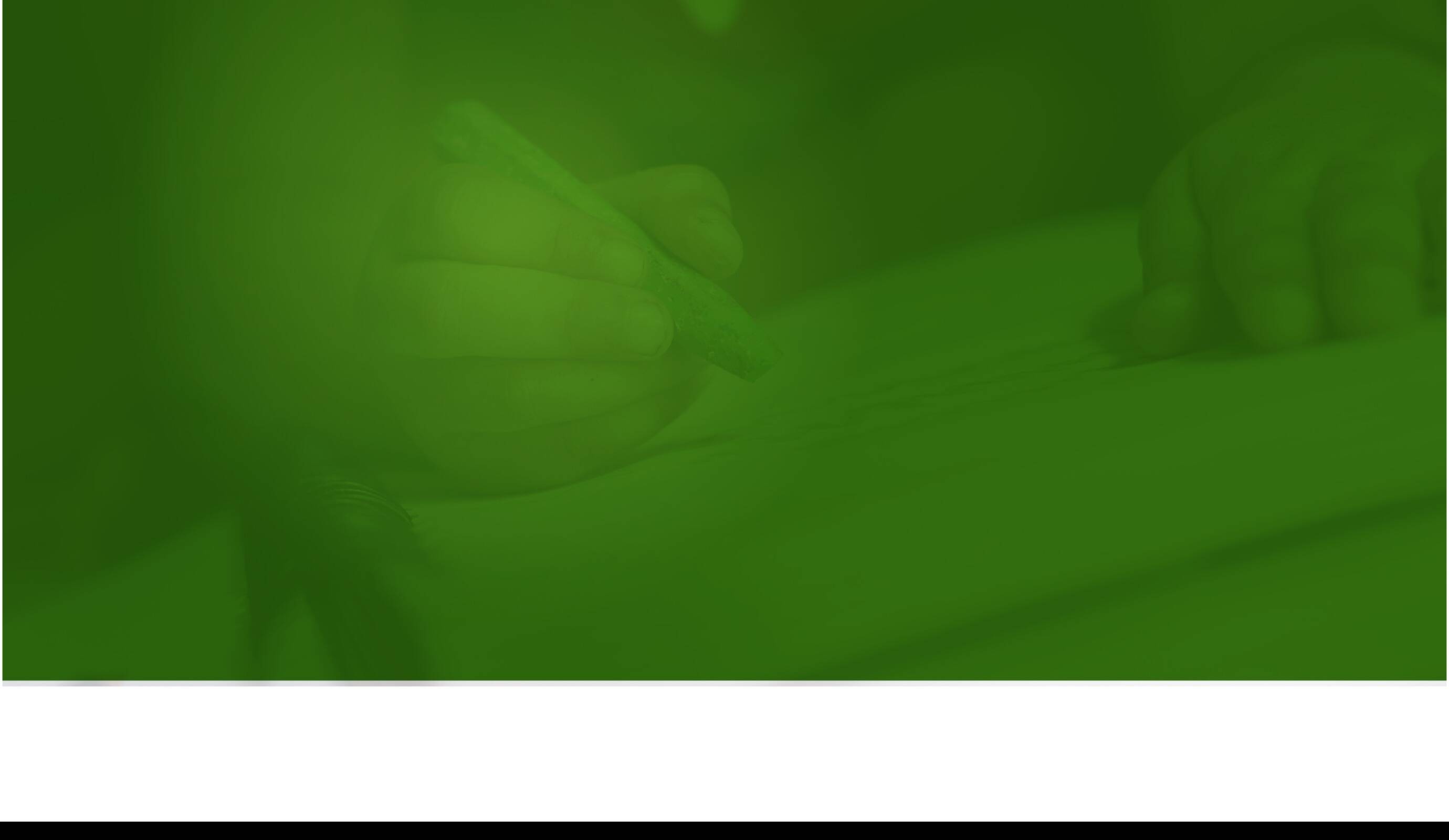
LC Packaging’s ambition and efforts have been mapped against the United Nations 2030 Agenda for Sustainable Development. In our daily operations, we directly contribute to Global Sustainable Development Goals nr 8, 12, 13 and 17. Indirectly, we touch upon 16 out of 17 SDGs.
Global agenda
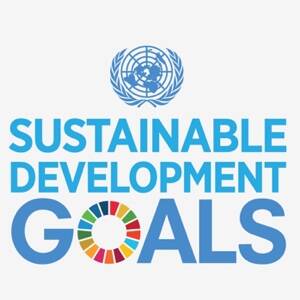
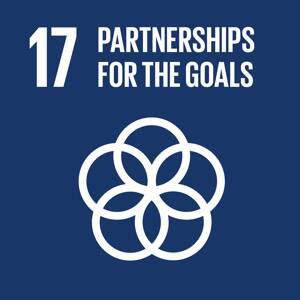
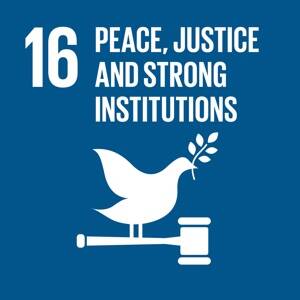
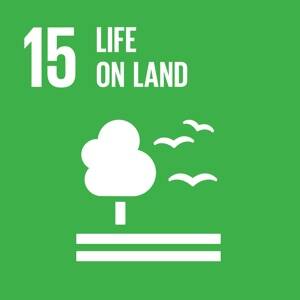
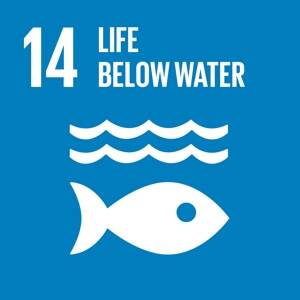
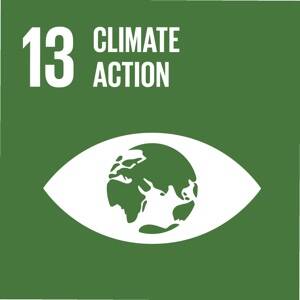
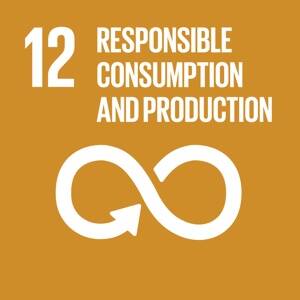
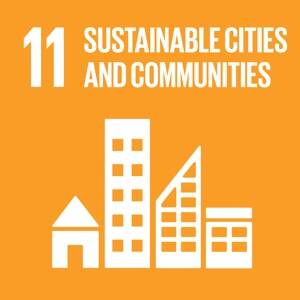
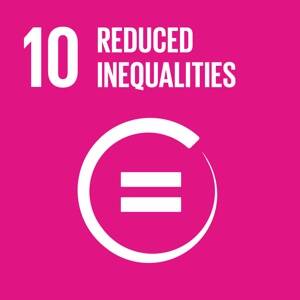
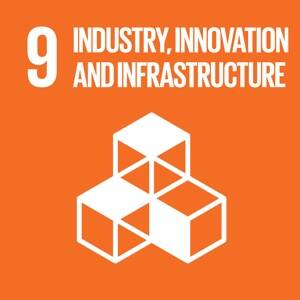
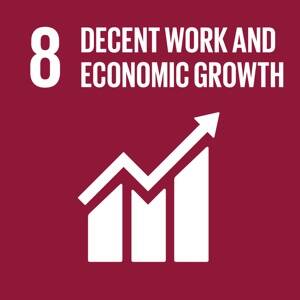
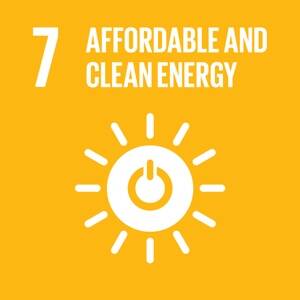
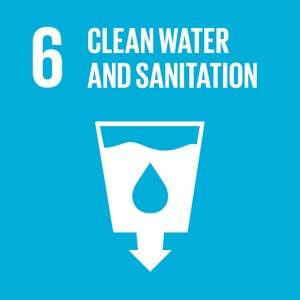
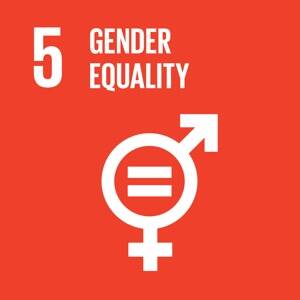
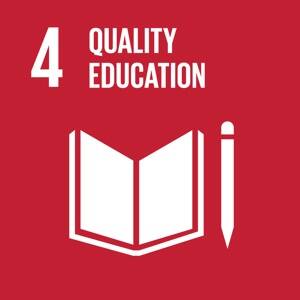
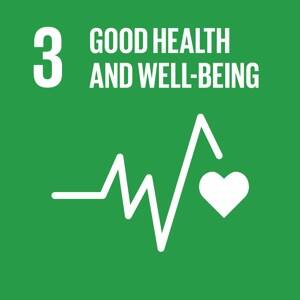
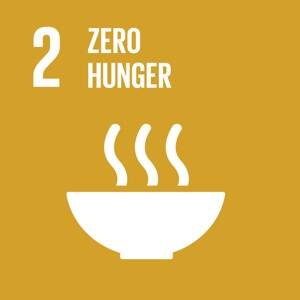
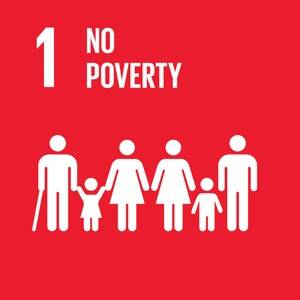
We are determined to improve the lifecycle of our packaging products one step at the time.
Developing sustainable
packaging solutions
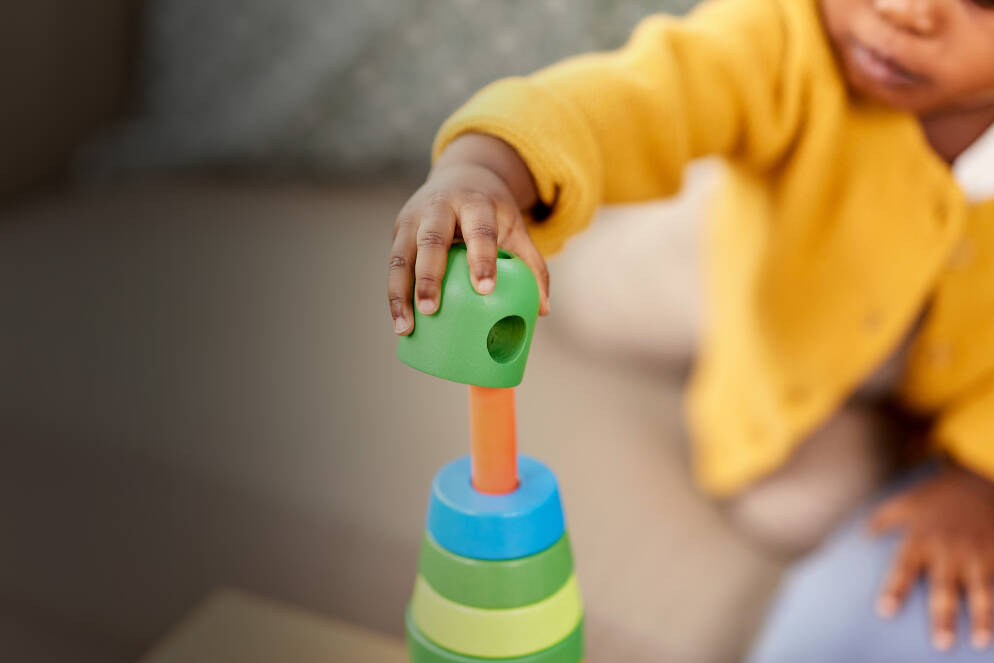
We have set ourselves 3 very ambitious and measurable goals for 2030 in which innovation and optimisation are key factors for success. By 2030, 80% of our revenue should come from products that deliver the circular economy, and we aim to have achieved a 50% emissions reduction from our value chain. Soon, we will expand our Research & Development activities by bringing missing knowledge in-house, and by seeking out new partnerships and external initiatives. Read more about our future ambitions in our 2030 Ambition magazine.
Initiatives and actions
Below we have summarised a selection of our initiatives to reduce the waste related to our packaging:
- Together with the Netherlands Institute for Sustainable Packaging (KIDV) we have performed a deep-dive sustainability analysis of our packaging portfolio and determined next steps towards delivering a circular economy.
- We have joined the Prevent Waste Alliance and the Plastic Pact Netherlands, thereby committing to help accelerate the transition to a circular economy: to do more with less plastic.
- To reduce the use of materials in our packaging, we have decreased the weight of our net bags with 3%-5%, saving approx. 40,000 KG of materials annually.
- We encourage the reuse of FIBCs with the help of our Worldbag reconditioning service, saving up to 10 KG of material per bag, when using the bag 5 times.
- Together with our customer Nestlé Portugal we have set up an on-site reuse project to significantly decrease the amount of plastic waste in its operations. The value of the project was recognised with the Nestlé Sustainability Award for Suppliers 2021.
- We have joined forces with colleagues in the industry in a working group organised by EFIBCA and EuroJute, to launch an Industry Design for Recycling (DfR) Standard for FIBCs. The DfR standard is expected to be taken into use in Q3 of 2022.
- To increase recyclability, we designed a Woven PP bag together with one of our valued customers, which is made of 98% polypropylene.
- With WPP bags that provide maximum stability during transport for one of our customers in the malt industry, we were able to reduce plastic use by 45% as extra hooder material was eliminated from the process.
- In 2019, we introduced 100% recyclable cardboard sleeves as an alternative to plastic wrapping.
- Our own production facility Dutch-Bangla Pack ltd. and our key production partners are now able to produce FIBCs with 30% recycled content. This has been achieved without having to increase the weight of the fabric, and the FIBCs remain as strong and safe as a bag from virgin material.
- To reduce process waste, in 2017, together with local partners, we initiated a first-of-its kind waste recycling project: GreenBangla. In 2021 we have recycled 503,606 KG through this GreenBangla initiative;
- We have teamed up with Veolia to minimise waste related to flexible packaging.
- Together with Starlinger & Co. GmbH we closed the loop on FIBCs by turning big bags into big bags once more for the first time. We also work together with Healix on producing high-quality rPP made from Post Consumer Recycling (PCR) materials.
- Together with our customer M.B. Nieuwenhuijse we have introduced plastic neutral bags.
Initiatives and actions
The two factors and measuring their success, and the fact that the goals itself is not measurably formulated, make it difficult to formulate just one outcome as a result for this goal.
- Since 2016, we have seen an annual increase in turnover. Since 2019, we annually report on the number of distributed packaging products, which has increased by 6% per year on average to 382 million products in 2021. The number of packaging products reused with the help of our in-house WorldBag reconditioning service has remained roughly the same over the past years. Based on these data, we assume that the total number of kilograms of materials used for our packaging has increased compared to baseline year 2016.
- This year we reported a decrease of the total KGs of materials used in our packaging of 18% since 2019 (first year of reporting). However, as our reporting data has become more accurate in 2021 and as some of the calculations made are still based on rough calculations, we choose not to draw conclusion from this.
- Compared to 2016 we have reduced the waste produced in our own operations with 72%. Over 38% of our waste is recycled with the help of our in-house waste recycling initiative GreenBangla, recycling up to 80% of our process waste at our FIBC production facility in Bangladesh.
- Additionally, in the past years we learned that there are many more elements impacting the waste related to our packaging, such as the reusability and recyclability of our packaging and the use of recycled content materials. Especially in these areas, we have made important steps and achievements.
Outcome
achieved
100%
Back in 2017, we decided success is to be measured by the outcomes of research on the total KGs of material use and waste produced in our operations in 2017 and 2022.
Measuring progress
GRI 301: 103-1, 103-2, 103-3
Sustainable solutions 2021: 103-1, 103-2, 103-3
Back in 2017, together with our production partners we were in the early stages of analysing existing packaging solutions on the type of materials used and the amount of waste related to these solutions in order to come up with more sustainable packaging.
Baseline
To minimise the waste related to our packaging, together with our Partners, we analyse, experiment with and optimise:
By 2022, we will have minimised the waste associated with our packaging.
Target
Sustainable materials
We have summarised a selection of our initiatives and actions to go above and beyond in protecting valuable goods from going to waste:
- Together with our customers we identify ‘product waste’ issues and new opportunities.
- All our packaging is tailor-made to suit the products’ properties and circumstances of transport and fits customer processes and technical demands.
- We have expanded our dedicated international in-house Quality department and have established a team of local quality managers to ensure our packaging is always manufactured according to the highest standards and passes the most stringent tests.
- We have installed ultramodern in-house testing facilities and have invested in cutting-edge technologies and clean room facilities.
- A centrally controlled quality management system (QMS) was implemented.
- To ensure quality even in times when travelling is not possible due to the COVID-19 pandemic, in 2020 we have put together a Remote Audit Programme, using remote controls, such as documentation and visual impressions, followed by video meetings.
- We score 8/10 on sustainable procurement and a 9/10 on Labour and Human Right in our 2021 EcoVadis Assessment, far above the industry average. Responsible sourcing and production, and good working conditions highly minimises the risk of quality issues and mistakes.
- Back in 2017, we have launched our Food Safe and Pharma Clean Assurance Programmes, offering the cleanest and safest packaging that meets the highest industry standards and is produced in our own state-of-the-art cleanroom facilities.
- In 2019, multiple top 5 players in the dairy industry among others, audited and approved our newly built 4,000 m2 state-of-the-art cleanroom with a 100% score for the manufacturing of high-care food.
- Our optimised Food safe and Pharma clean big bags and clean-room big bags meet all standards for clean packaging and are hygienic, odourless and minimise the risk of antistatic discharges.
- Literally a breath of fresh air! Protective, but flexible and breathable packaging, such as net bags, and our ventilated big bag, prevent for example onions and seed potato from sweating and rotting in transit; all developed in-house.
- Our technical textiles protect crops from animals and adverse weather conditions.
- For products such as powders and granulates, the form-stable QBag was designed protecting products from any leaks during filling, storage, transport and discharge.
- WPP bags – in which we are a global leader - with a block bottom also provide better filling properties and a stand-up capacity.
- To protect products against oxygen, water vapor and UV, our big bags and WPP bags can be fitted with a protective inner liner.
- Shelf ready packaging reduces the risk of valuable products as it eliminates a whole packaging cycle. This type of packaging serves as transport packaging, and when arrived at the marketplace it can be placed directly on the shelves of the store.
We aim to continue to excel in our core business of deliver safe and reliable (transport) packaging for dry bulk goods with sustainability at the top of our agenda.
Initiatives and actions
Looking back, this goal should not be a goal, because this is what we do at the core of our business: protect valuable goods from going to waste during its journey through the supply chain. Furthermore, this target was unclearly formulated and is therefore not directly measurable. We have therefore decided to measure the achievement of this goal by the number of developments that have taken place to protect the products we package even better: our efforts to go above and beyond.
Outcome
Success is measured by the intensity and success of our sustainable packaging solutions to prevent the waste of products during storage and/or transportation.
Measuring progress
achieved
100%
Sustainable solutions 2021 : 103-1, 103-2, 103-3
GRI 416 : 103-1, 103-2, 103-3
Back in 2017, we were already working on several initiatives to prevent the waste of products during storage and transportation, such as, for example, the ventilated big bag, that allows its cargo, like potatoes or wood logs, to breath and prevents contamination. Also, we provided special bags for transport, and storage, for example, safe and clean food packaging to safely transport milk powder.
Baseline
Quality packaging protects the environmental, social, and economic investment in products and contributes to economic development and social well-being by facilitating the distribution and delivery of products to the marketplace in pristine condition.
Target
By 2022, we will have significantly reduced the waste of (food) products during storage and transport in our packaging.
Sustainable solutions
We have set ourselves 3 very ambitious and measurable goals for 2030 in which innovation and optimisation are key factors for success. By 2030, 80% of our revenue should come from products that deliver the circular economy, and we aim to have achieved a 50% emissions reduction from our value chain. These goals can only be achieved when sustainability, in addition to quality, plays a leading role in all our innovation activities, and when innovation itself becomes a top priority on our corporate agenda. When we do so we can, for example, create our circular packaging portfolio, make production processes more sustainable, and optimise and innovate our activities and services. Soon, we will expand our Research & Development activities by bringing missing knowledge in-house, and by seeking out new partnerships and external initiatives. Read more about our future ambitions in our 2030 Ambition magazine.
More data in our 2021 Solutions Report
Future ambitions
A selection of our innovative initiatives and actions for more sustainable operations and packaging solutions:
- In 2017, together with local partners, we initiated a first-of-its kind waste recycling project: GreenBangla. The initiative was recognised by the UN Global Compact Network Netherlands in their SDG Progress Report 2018 ‘Companies on the way to 2030’. In 2021 we have recycled 503,606 KG through the GreenBangla initaitive.
- To increase recyclability, we designed a Woven PP bag together with one of our valued customers, which is made of 98% polypropylene.
- To reduce our CO2 footprint in 2018, we focused on more sustainable container loading solutions together with our production partners. By making small adjustments to PP bags, we created 6% more container capacity, and by pressing Leno bag bales tighter, we created up to 20% more loading capacity; saving 25 containers being shipped per year.
- In 2019, we introduced 100% recyclable cardboard sleeves as an alternative to plastic wrapping.
- With WPP bags that provide maximum stability during transport for one of our customers in the malt industry, reducing plastic use by 45% as extra hooder material was eliminated from the process.
- In 2020 we launched our HSI (How Sustainable Is…) Programme to identify key components for a sustainable future for our packaging solutions, resulting in a short-term and long-term road map for R&D to make our packaging deliver the circular economy.
- Our own production facility Dutch-Bangla Pack ltd. and our key production partners are now able to produce FIBCs with 30% recycled content. This has been achieved without having to increase the weight of the fabric, and the FIBCs remain as strong and safe as a bag from virgin material.
- Together with our customer Nestlé Portugal we have set up an on-site reuse project to significantly decrease the amount of plastic waste in its operations. The value of the project was recognised with the Nestlé Sustainability Award for Suppliers 2021.
- Our LC Ireland branch partnered with Marlet Property Group for the development of a high-quality, innovative, and environmentally sound solution for waste management in residential areas.
- We have invested in greening our production through energy efficient machinery, sustainable building materials, LED lighting, and electric vehicles among others. Read more about our sustainable production.
- Additionally, several LC Packaging warehouses have replaced their machinery with new printers that will not only offer higher quality prints, but also enable us to switch from solvent-based ink for polypropylene bags to water-based ink.
- In 2020 we finished the build of our new, BREEAM Outstanding certified Head Office that was build with sustainability in mind, contributing to the environment in a positive way.
Initiatives and actions
The two factors and measuring their success make the result for this goal difficult to formulate just one outcome. Looking at the number of initiatives and projects deployed over the past five years; we have innovated and optimised our products, infrastructure, and services, and we have started partnerships to reach our goals, which have led to innovative solutions. In all initiatives and projects, sustainability is a key factor in the decision-making process.
The second metric of measuring success that we had identified back in 2017 was the percentage of turnover coming from sustainable packaging solutions. For this, our baseline year ultimately became 2019, as this was the first year. We measured the percentage of turnover coming from recyclable packaging (83%), which we at that time identified as ‘sustainable packaging’. As throughout the years, we evolved the definition for recyclable packaging twice – in 2020 based on input through our partnership with Veolia and in 2021 based on a deep-dive analysis of our packaging portfolio in cooperation with the Netherlands Institute for Sustainable Packaging (KIDV) - the metric was measured based on different standards over the years and therefore not suitable to measure the results of this goal.
In 2022, we have adopted the definition for sustainable packaging as defined by the Sustainable Packaging Coalition (SPC), based on 8 criteria for sustainable packaging.
Our success is measured by two factors: 1) the number of initiatives/projects in which sustainability was a key factor, and 2) the percentage of turnover coming from sustainable packaging solutions.
Measuring success
Although sustainability was an important topic on our agenda back in 2017, we did not yet fully integrate this topic into our innovation processes and decision making.
Innovation 2021: 103-1, 103-2, 103-3
Sustainable solutions 2020: 103-1, 103-2, 103-3
Outcome
Baseline
We believe optimisation and innovation is key for the future of our company, our employees, our partners, and our customers. We focus on improving infrastructure and our operations and creating innovative packaging solutions that support our customers as they seek to meet the needs of their consumers, while also reducing the impact on the environment.
By 2022, sustainability will be fully integrated in our innovation processes, leading to sustainable operations and packaging solutions.
Target
Innovations